Traditional cam lobe motors used in skid steer loaders can often cause shock responses, poor energy usage and speed restrictions. Designed to solve these limitations is Danfoss’ Thorx range
Owners and operators increasingly look for machinery that improves productivity. Skid steer loaders are prime examples. To pick up heavier loads, complete tasks faster, and increase travel speed, skid steers are being designed to deliver higher power and greater force. Meanwhile, more attention is being paid to operator comfort. Smooth, predictable operation is no longer a desire – it’s a demand.
High-pressure hydraulic pumps are delivering the power skid steers need, and the market is shifting to cam lobe motors to complement the performance of these pumps. Cam lobe motors offer higher pressure ratings and greater efficiency than other technologies, delivering 30% more force. However, cam lobe motors have historically fallen short when it comes to two-speed shifting, package size, and efficiency throughout the speed range.
Two-speed motors support the industry drive for greater productivity, delivering higher torque when working and higher speed when roading. But a problem arises when shifting between the two. A sudden change in the wheel speed or torque can create a jarring shock response, resulting in machine instability and even a lost load. The effect is worse when the machine is cold. Shocks can be erratic or delayed, undermining driver confidence.
With motors positioned back-to-back in skid steer loaders, length is also important. Typical cam lobe motors have a large envelope, which can make assembly and service a challenge in compact machines.
Finally, starting efficiency and maximum speed efficiency can be a problem for cam lobe motors. When a machine is stationary, torque efficiency is low, creating a weakness in machine performance. Also, the heat generated at maximum speed makes the machine hot and wastes energy on cooling.
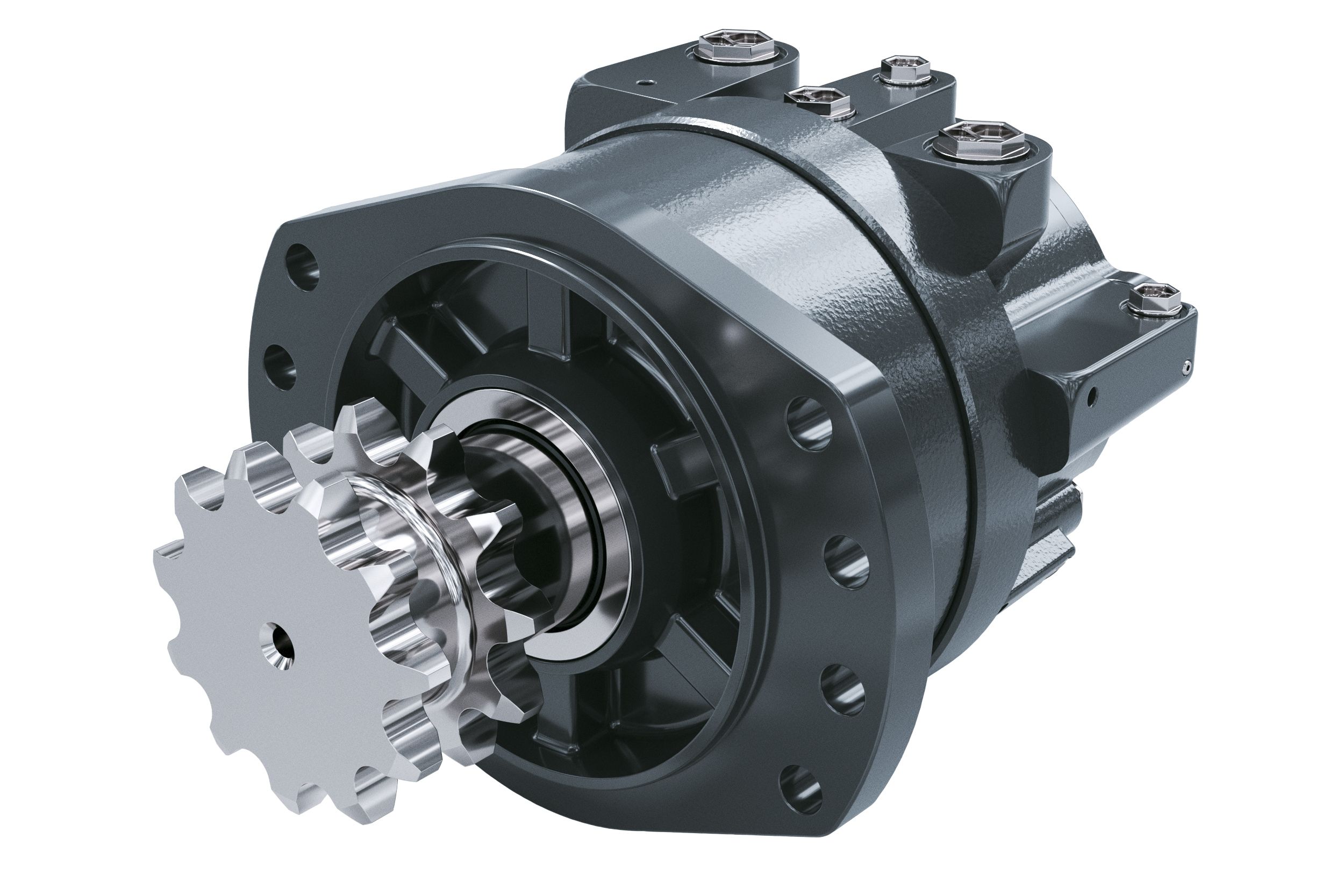
Danfoss Power Solutions’ new Thorx line of cam lobe motors solves these challenges. The CLM 8 S and CLM 4 S cam lobe motors — designed specifically for construction machinery with chain drives, such as skid steer loaders, are now available. Models for other drive types are coming soon.
Danfoss Thorx motors feature newly developed two-speed technology which reduces shock at speed changeover by 70% and eliminates inconsistencies due to temperature, resulting in smoother, more predictable machine handling.
Thorx motors feature a larger diameter rotary group that enables the parking brake to be integrated in the center, rather than bolted to the rear. This configuration makes the motors 33% shorter in length than other chain drive motors, with only a one-centimeter increase in width. Reducing the motor’s space claim simplifies installation and frees OEMs to increase the size of the chains driving the wheels, which can increase the life of the machine.
The increased space created by the larger rotary group enables a return to proven multidisc brake technology, which offers strong parking torque as well as smooth emergency stopping. Unlike dog clutch brakes, which produce harsh emergency stops and wear out extremely quickly — sometimes in as few as one or two stops — the Thorx motor’s brake is designed to withstand at least 100 dynamic emergency stops.
Another advantage of the motor’s larger rotary group is reduced friction and flow losses, which increases the starting efficiency as well as high-speed efficiency by 5%. Operators can achieve faster travel speeds or use less power at the same speed while wasting less energy in the form of heat.
Danfoss Thorx motors have reinvented cam lobe technology, eliminating shortcomings while maintaining the technology’s strong points. All motor technologies have their place, and with its complete motor portfolio, Danfoss has the right technology for the application, ensuring a perfect match.
Images: Danfoss Power SolutionsÂ
This article first appeared in the March 2025 edition of iVT Interntional