Swedish OEM Eco Log helped put the very first Volvo Penta engine in a forestry application. A decade later, this Volvo Penta D8 Stage IV engine is still running and the 1,000th Volvo Penta-powered Eco Log machine has been delivered.
Almost 10 years ago, the first Eco Log 580E Harvester was fitted with the first Volvo Penta engine ever installed in a forestry application and sold to Swedish forestry specialists Nitta Rundvirke AB. In 2024, when Nitta Rundvirke ordered another harvester, the Eco Log 590G with the latest D8 EU Stage V Volvo Penta engine, the sale marked a new milestone in the companies’ long-standing relationship, as well as the delivery of the 1,000th Eco Log machine powered by Volvo Penta.
Frans Spetz is one of the co-owners of Nitta Rundvirke, located in western Sweden. Founded in 1965, the family-owned company operates in several industries, including transportation, excavation, and forestry. In addition to running his company, Spetz conducts a lot of field tests.
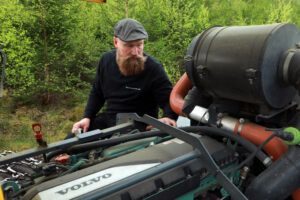
Extensive testing in demanding work environments, combined with an ongoing dialogue on improvements, is essential for finding the best solutions. By working in close collaboration with customers, Volvo Penta develops products and services that meet ever-increasing demands in terms of productivity, cost-efficiency, connectivity, and sustainability. With Nitta Rundvirke, new engines and machines are tested in various forestry applications, in their proper work environment.
“As field testers, we are honest and straightforward throughout the development process,” says Spetz. “There are other field testers that are just happy to try something new, without giving proper feedback or telling the manufacturer what they actually think. But we always do.”
Among the machines that the operators of Nitta Rundvirke work with, and have tested thoroughly, are those of Swedish OEM Eco Log, equipped with Volvo Penta industrial engines. Spetz bought his first Eco Log 580E Harvester almost 10 years ago, outfitted with the very first Volvo Penta engine ever installed in a forestry application. More than 11,000 work hours later, that D8 Stage IV engine is still running today, in the same harvester, with only routine maintenance since its installation.
When a forestry machine malfunctions in a remote location, the operator will often have to solve the issue on the spot. To keep costly downtime to a minimum, they need to know a lot about their machines and their engines.
Spetz and his colleagues use their machines to their maximum capacity. Even so, the D8 engine has remained robust and reliable year after year.
“We had to change the water pump at some point,” Spetz notes. “But that’s the kind of inevitable maintenance that comes from normal wear and tear.”
Forestry machines are very complex, and operators demand a lot from them. However, the construction of both the machines and their engines needs to be intuitive and convenient, to facilitate maintenance when required.
“When you dimension everything correctly, and the engine is easy to work with, it just makes everything a lot easier,” Spetz says, adding that one of the reasons many players in the forestry industry choose Eco Log’s machines because they are equipped with Volvo Penta engines.
In the spring of 2024, Spetz ordered yet another harvester, the Eco Log 590G, equipped with the latest D8 EU Stage V Volvo Penta engine. Shortly afterwards, he saw a video acknowledging the delivery of the 1,000th Eco Log machine powered by Volvo Penta.
“There was a clip highlighting the occasion, showing Volvo Penta coworkers displaying an engine with a shiny, gold-coloured engine cover, which I thought looked really nice,” says Spetz.
When Spetz met with Eco Log and Volvo Penta to receive his new harvester, he was greeted by an unusually great number of people out in the forest.
“They had brought cake and stuff, and there – under the hood of my new harvester – was the engine with the golden cover.”
“The engines just keep going, meaning that we can keep going, too,” says Spetz. “No repair needed, only occasional routine maintenance. It’s cool to know that the 1,000th engine sits right there, in our harvester. Not that we get that many opportunities to look at it, since it rarely ever needs to be checked.”