An in-depth look at some of the best new vehicles that will be on display at Bauma in Munich next week (7-13 April 2025), as selected by iVT editors. Keep watching this space for more highlights and new announcements in the days to come
Liebherr L 566 H
Hydrogen wheel loader and autonomous drive
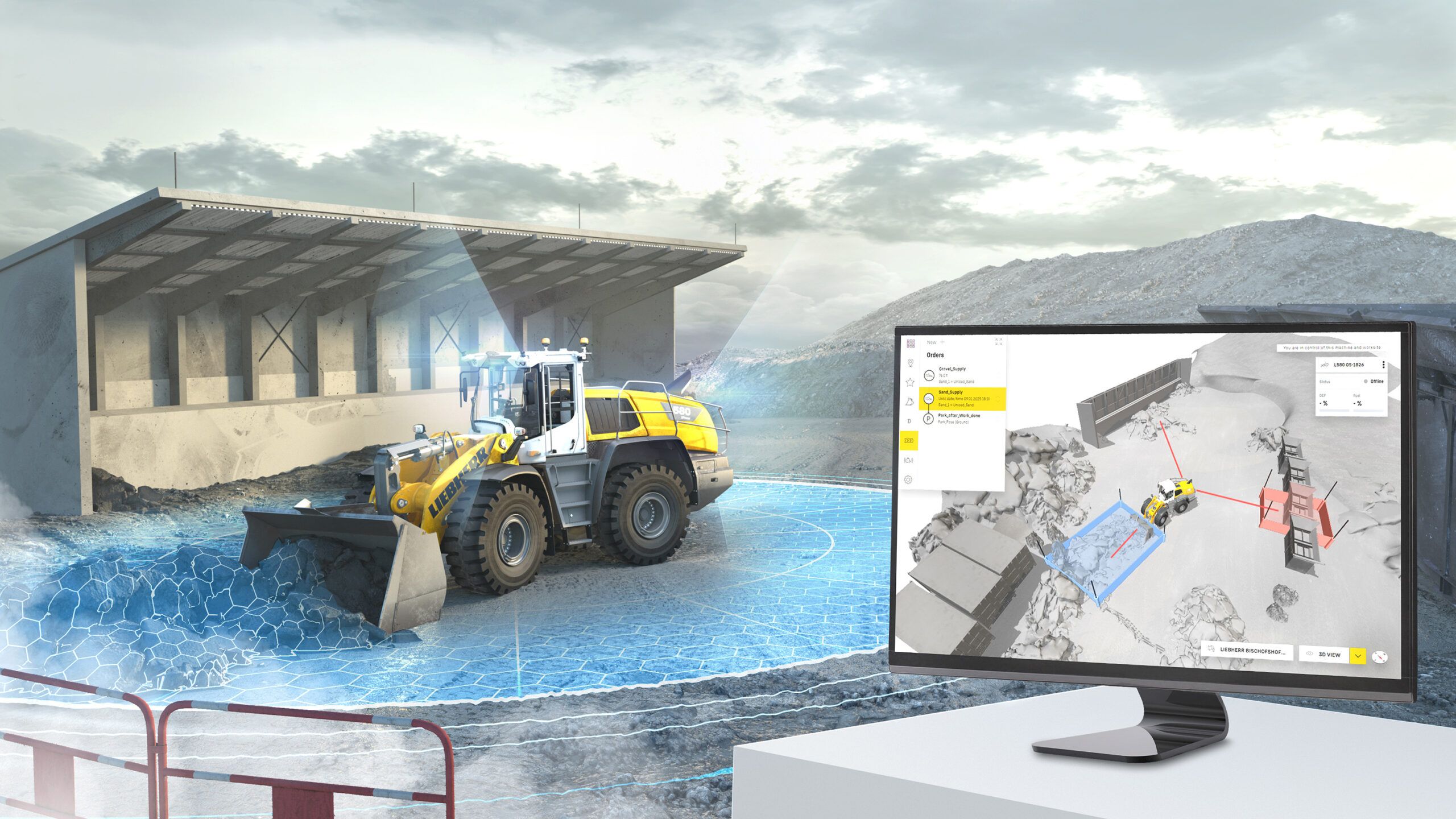
Stand FM.810
The vast Liebherr stand is always a centrepiece for Bauma, with a huge range of vehicles certain to grab attention. Chief among them this year will be a hydrogen-powered prototype, the L 566 H, featuring a fully autonomous operating system for it and other wheel loaders.
The L 566 H is the first large wheel loader equipped with a hydrogen combustion engine. Based on the L 566 XPower, the machine is to undergo a two-year trial at Strabag’s Gratkorn quarry in Austria, where it is projected to reduce CO2 emissions by up to 100 tonnes annually – equivalent to about 37,500 litres of diesel.
“We are working very closely with Strabag to figure out the logistics of hydrogen delivery and storage at construction sites,” says Larissa Luntz, Liebherr’s head of public relations. “We’ve installed a fuelling station at the test site to understand the costs and infrastructure requirements.”
The company is also introducing Liebherr Autonomous Operations, a system that enables driverless wheel loader operation for repetitive tasks. This has made it to the final three of the Digitalization category in the Bauma Innovation Awards, with the winner to be announced on the evening before Bauma opens.
“You don’t need any special IT skills to initiate the wheel loader deployment. The system is very intuitive and requires only a few inputs for the job,” says Dr Manuel Bös, head of emerging technologies at Liebherr. The machine uses 3D environmental sensors to navigate and can operate without GPS reception, making it suitable for indoor and underground use.
The autonomous system builds on existing safety features. “Last time at Bauma, we showcased some assistance systems like our braking assist and obstacle recognition technologies. These form the foundation for autonomous operation,” says Luntz. “We started with operator assistance, and now we’re moving towards fully autonomous capability.”
Operators can switch between manual and autonomous operation. The system is designed to reduce component and tyre wear while lowering overall fuel consumption through consistent operation patterns.
Visitors to Liebherr’s stand will be able to see live demonstrations of the autonomous wheel loader throughout the day, while the hydrogen-powered L 566 H will be on display. Both machines are part of the company’s ongoing work to develop practical and efficient solutions for reducing emissions and increasing automation in construction equipment.
HG E2000 e
Bauma’s most efficient articulated powertrain
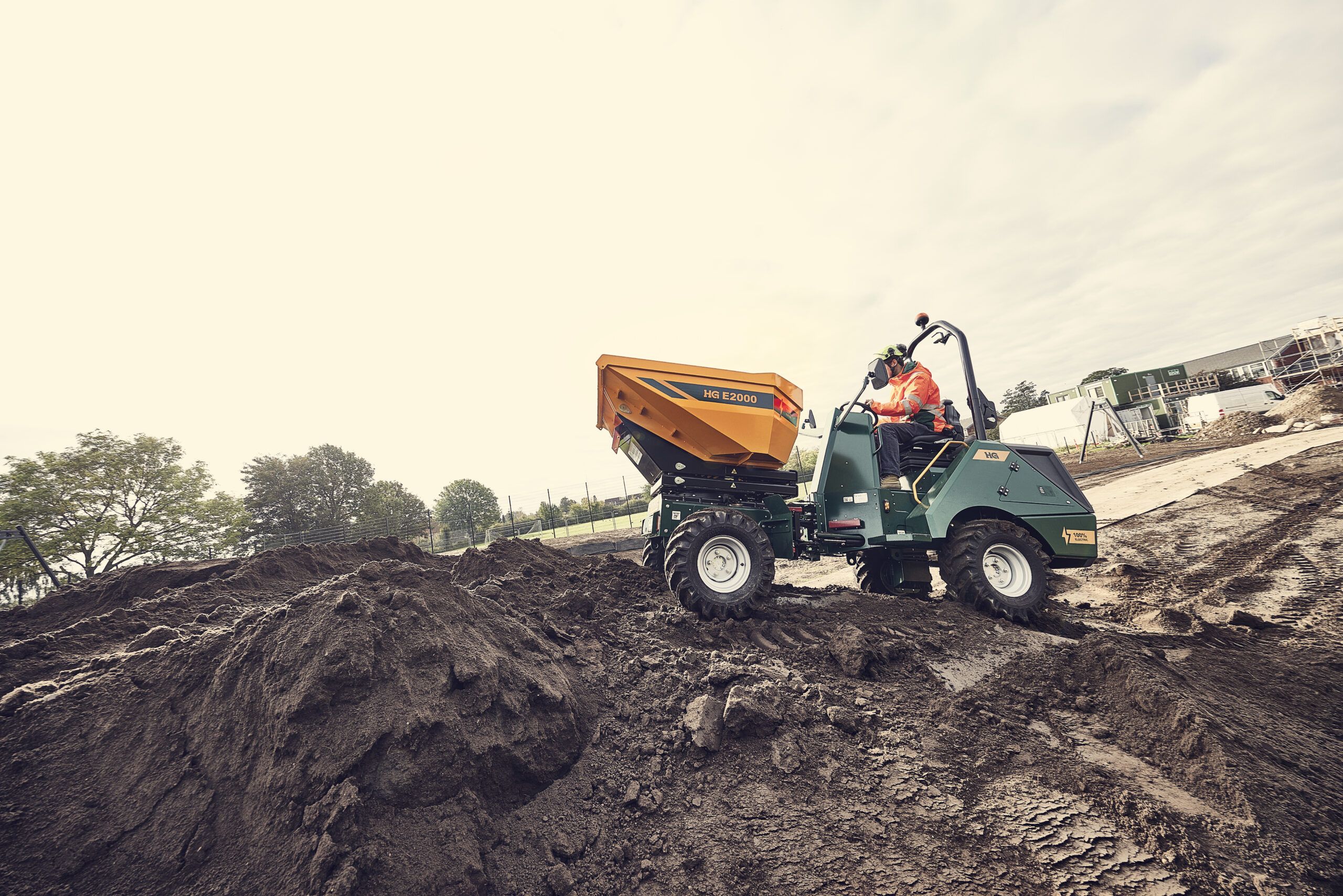
Stand B5.445
Danish manufacturer HG is making at its first-ever Bauma appearance and showcasing its E2000, an all-electric two-ton dumper that uses in-wheel motors to create what the OEM believes is the most efficient powertrain ever created for an articulated vehicle.
The E2000 can operate for up to 12 hours on a single charge – a feat that CEO Nikolaj Birkerod attributes to the company’s unique approach to electric drive technology.
“We decided to work differently,” explains Birkerod. “Instead of converting power from a battery through a traditional transmission unit, we have four individual motors, one in each wheel. Depending on how the machine turns and at what angle, each wheel uses just the right amount of energy during driving. This results in 50% less energy consumption compared to other electric machines in the market.”
This innovative wheel-motor system required significant development in software control systems. “The wheels need to coordinate exactly how they are turning backward, forward, at what speed and what force,” Birkerod notes. “From a coding and software point of view, we need to have an answer for every given situation to keep it running smoothly.”
The E2000’s practical features include high swivel tip functionality for precision unloading and one-pedal driving for enhanced operator comfort. The machine can be charged from 20% to 80% in just 2.5 hours using either a 400V industrial connection, 220V EU plug, or a Type 2 car charger, offering flexibility for various work environments.
Before its international debut at Bauma, HG conducted extensive field testing in Denmark, with 25 units operating for a year and a half. According to official Danish authority calculations, the E2000 offers a 10% cost advantage over conventional alternatives over a seven-year period, making it an economically attractive option for construction companies looking to transition to sustainable equipment.
Volvo CE EC230
Updated and upgraded 23-tonne battery excavator
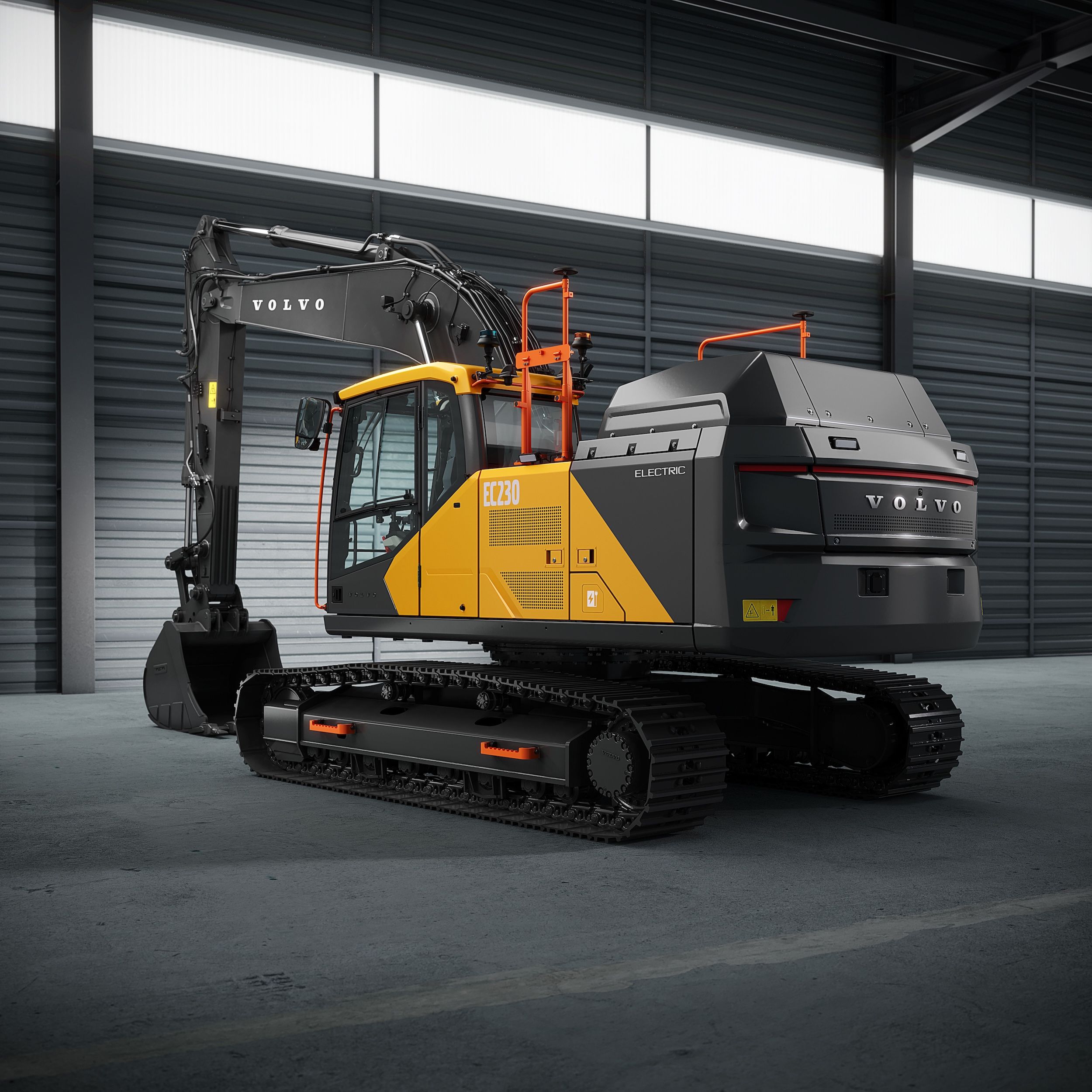
Stands C6.313 & FM.HOF 60C.2
Volvo Construction Equipment is keeping the covers tightly on its all-new zero-emission machine, which won’t be unveiled until the second day of Bauma, at 10am on 8 April. However, just before this edition of iVT went to press the OEM did reveal some details of its new lineup that will be launched in Munich, including an update to its EC230 Electric excavator. The EC230 is just one vehicle in what will be a 100% zero-emission line-up at Bauma – an industry first for a major OEM.
At an impressive 23 tonnes the EC230 is currently the largest battery electric vehicle in Volvo’s range. The updated version will offer extended operating times of 7-8 hours per charge, powered by a 600V lithium-ion battery with a 450 kWh capacity. The machine can reach 80% charge from 20% in one hour using a 250-kW charger.
“The first-generation EC230 Electric provided valuable customer insights and market feedback which played a pivotal role in shaping this new generation model,” says Kurt Deleu, head of excavator product management at Volvo CE.
Bill Law, senior VP at Volvo CE, agrees that the challenges of electrification have changed the traditional vehicle development cycle. “With some of these machines, we do what we call a customer pilot launch program,” says Law. “This is where we do very small launches, not high volume, learn all we can, bring them back in, update them quickly and then get them out again.”
The excavator incorporates the company’s new-generation features, including an enhanced cab environment, an intelligent electrohydraulic system, and HD Volvo Smart View with people and obstacle Classification. The hydraulic efficiency has been improved by 10%.
Looking to the future Law emphasizes Volvo’s commitment to zero-emission machines in all their forms, while also catering for diverse market demands: “We believe in transformation and battery electric – possibly fuel-cell electric going forward. We also understand that not everybody is on the same speed and journey in different markets, countries, or segments.”
Mecalac Revo990
Rotating-cab backhoe
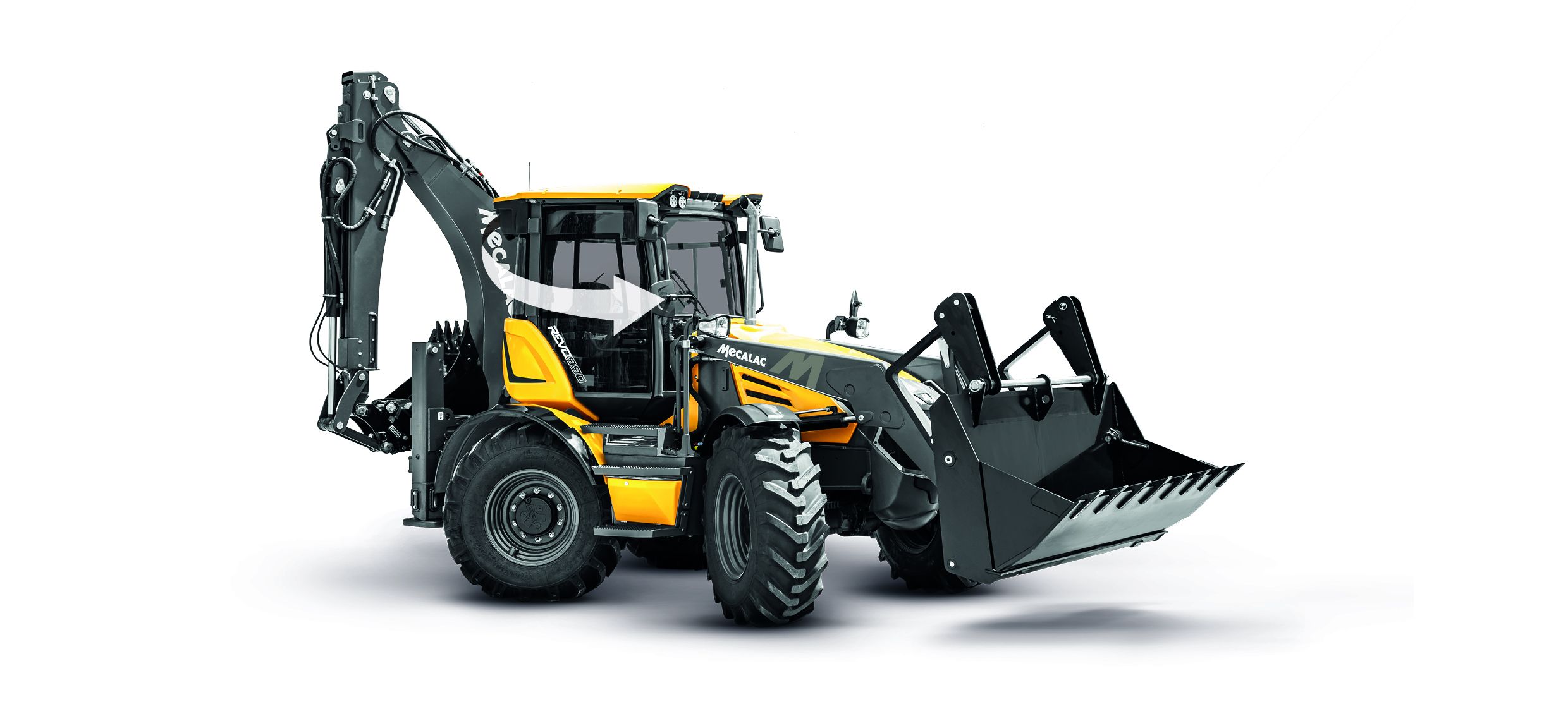
Stand FM.711/2
Turning heads on the Mecalac stand will be its brand-new backhoe loader, the Revo990, featuring a cab that rotates as a complete unit, overcoming limitations of the traditional fixed-cab design where operators must turn their seat to switch between operating the front loader and rear excavator.
“To go from loading position to excavating position on a traditional backhoe, there are around 17 actions – putting the steering wheel up, putting the seat back, turning the seat, putting on the park brake…” says Patrick Brehmer, Mecalac’s head of design and product management. “With the Revo990, it’s one single action with one finger, and in three seconds you turn your cab and you’re facing the right way for either excavating or loading.”
The rotating cab design offers practical advantages beyond operator comfort. The machine can be driven with the cab in any position, which is particularly useful for operations like ditch cleaning along roads where the operator needs to see the work area while moving the machine.
The redesign also allowed Mecalac to lower the engine position, improving forward visibility for loading operations. All driving controls remain accessible regardless of cab position, allowing operators to move the machine while maintaining their preferred orientation for the task at hand, updating a vehicle design that has remained largely unchanged since its introduction in the 1950s.
The Revo990 will be displayed alongside other new Mecalac machines at Bauma 2025, including an updated 12 Series range and additions to their electric machine lineup. The company’s 1,500m2 booth will feature 27 machines, with 500m2 dedicated to equipment demonstrations.
Manitou
Rotating telehandler hydrogen fuel-cell prototype
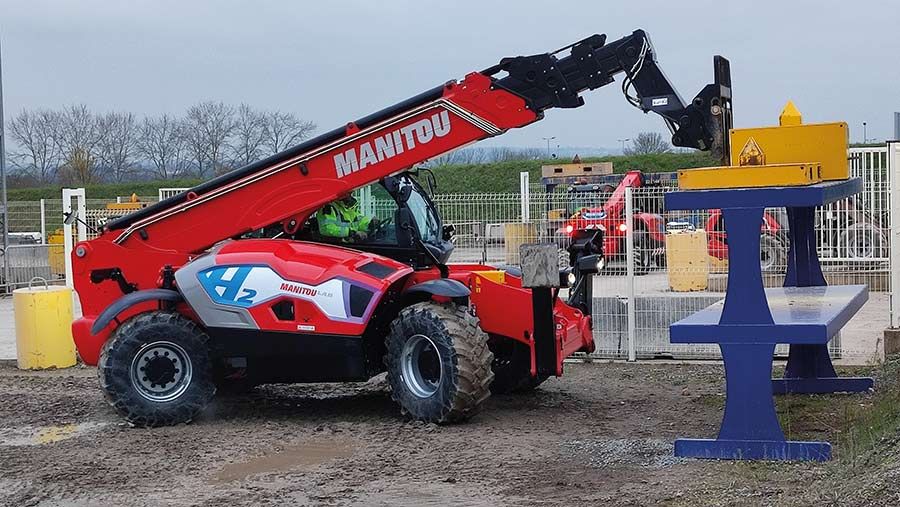
Stand FS.908 /1
Manitou Group will showcase a new hydrogen fuel-cell-powered telehandler concept at Bauma, with full details available when the covers are pulled off the vehicle on the first day of the fair.
“Innovation is at the heart of our DNA. We have always been innovative, pioneering,” says Frank Lethorey, Manitou communications manager. “This step is concrete and is a realistic alternative to diesel and battery electric. Manitou Group is a key player in decarbonization and is working on hydrogen technology for telehandlers. The modularity of our electrical products directs us now towards the fuel cell technology. This prototype is based on our electrified machines, which already meet the same specifications as their combustion-powered predecessors (apart from range).”
The second-generation machine will build on technology from Manitou’s first hydrogen fuel-cell prototype, unveiled in December 2022. This first machine was a fixed telehandler with 18-metre lifting height and 4-tonne load capacity, running off green hydrogen from a station located at Mantiou’s own test centre. “This second prototype will be a rotative telehandler,” reveals Lethorey. It is promised that the new machine will also run off green hydrogen.
“The overall CO2 balance potentially better than electric, depending on how H2 is produced. At Manitou Group, we definitely focus on green hydrogen,” says Lethorey. “There are no CO2 or particulate emissions with hydrogen fuel cells. Moreover, this powered energy on-board range is similar to electric, with a recharging time similar to diesel. And we have the possibility of recharging with mobile off-grid stations.”
The new vehicle will add to the company’s growing zero-emission portfolio, demonstrated across the 25 machines from both Manitou and Gehl which will be shown on the 1,600 m² outdoor stand. Among these innovations will be two electric high-lift telehandler models. Designed for full-day operation while complying with stringent low emission zone regulations, the new ME 430 Lift electric forklift with lithium-ion batteries and a 3.5-tonne capacity, and the new 30kW fast charger for the MT telehandler and ME Lift electric ranges are scheduled for release in Q2 2025. “We’ll have a large area dedicated to our low emission solutions,” says Lethorey.
Komatsu PC7000-11E
The electric giant
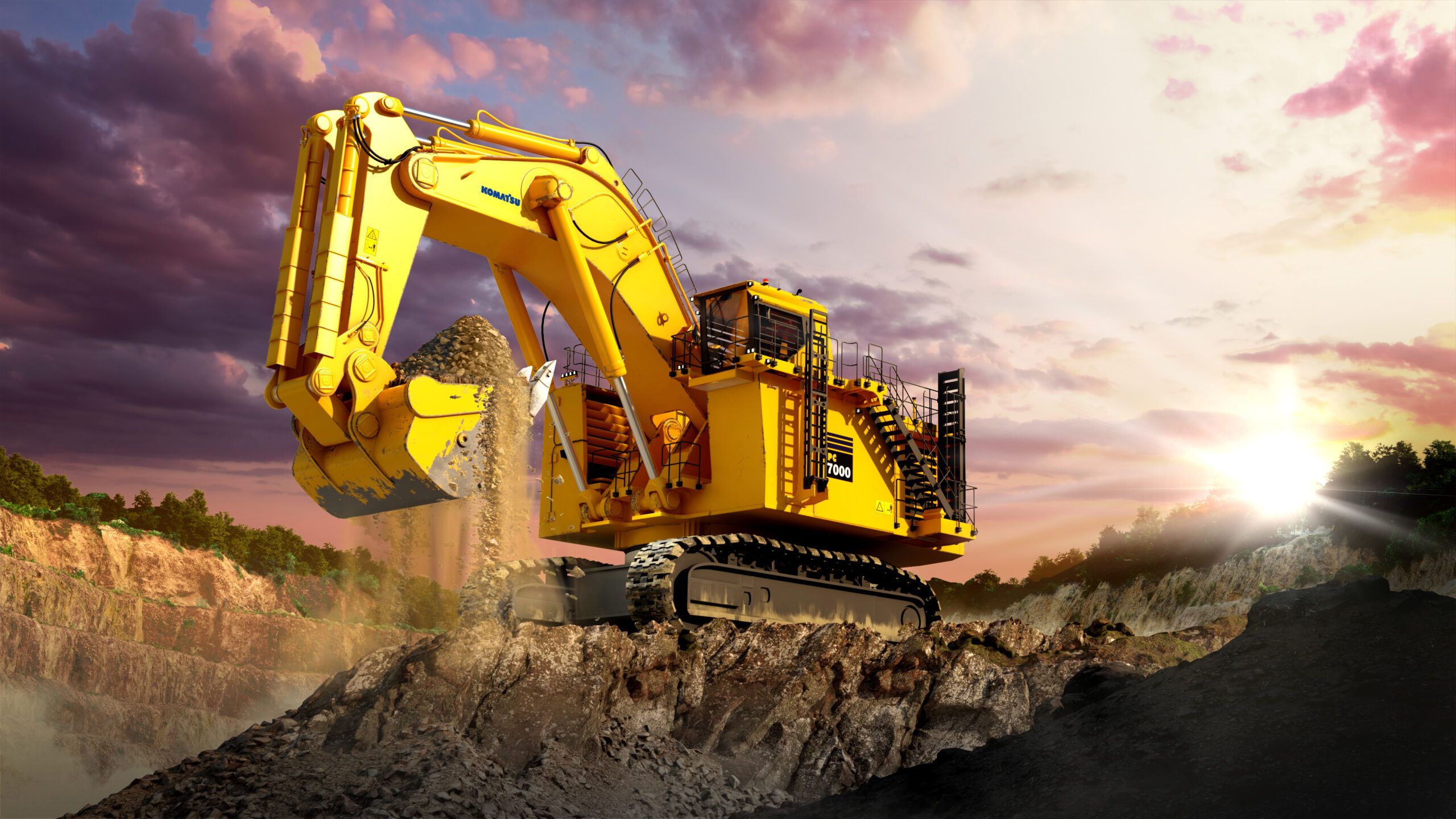
Hall C6 and Stand FM.713/1
At Bauma, Komatsu will be demonstrating what’s almost certain to be the largest electric machine at the event – a 692 tonne, cable-electric PC7000-11E hydraulic mining excavator in backhoe configuration.
The PC7000-11E aligns with Komatsu’s commitment to sustainable mining solutions. Equipped with a class-leading 44m³ bucket, the cable-connected electric excavator is designed to work with Komatsu’s mining truck range from the 730E up to the 980E models.
“Lots of big mining customers are requesting electric machines as they aim to go zero emission,” says Marc Blondeel, communications manager at Komatsu. “For that, we have a solution for every model we are manufacturing for mining, starting from PC3000 up to PC8000. Every model is available as an electric version.”
The electric drive technology reduces carbon footprint by up to 95% compared to diesel equivalents. Operating costs are significantly lower, too, with the elimination of diesel fuel and reduction in parts, maintenance, and lubrication costs resulting in up to 50% savings in TCO compared to conventional diesel drives.
One challenge with electric backhoe excavators as large as the PC7000 has been cable management. “The difficulty is a backhoe machine is always moving backwards, and the cable is coming from the back,” says Blondeel. “So there’s a small risk to the cable.” Komatsu has overcome this with a fully automatic cable drum to make manoeuvring in the pit safer and easier.
The PC7000 is just one of 34 machines Komatsu will be presenting across more than 7,500m2 of exhibition space, including 13 new models such as the PC220LCi-12 excavator featuring new iMC 3.0 integrated machine control technology, and a completely redesigned cab; and the new WA475-11 and WA485-11 wheel loaders with increased payload, bucket capacity and enhanced fuel efficiency
The company’s indoor demonstration at Bauma will focus exclusively on its wide range of electric machines, including the PC33E-6, pre-production models PC20 Electric and PC26 Electric, market pilots PC138E-11 and the PC210LCE-11, as well as several concept machines.
Visitors can also explore Komatsu’s digital solutions, including Smart Construction, Smart Quarry, and a full suite of telematics solutions designed to optimise site operations through data-driven decision-making. Plus, the OEM has promised a host of new machine announcements during the week of the highly anticipated event itself.
Hitachi ZE300
Hydrogen combustion excavator
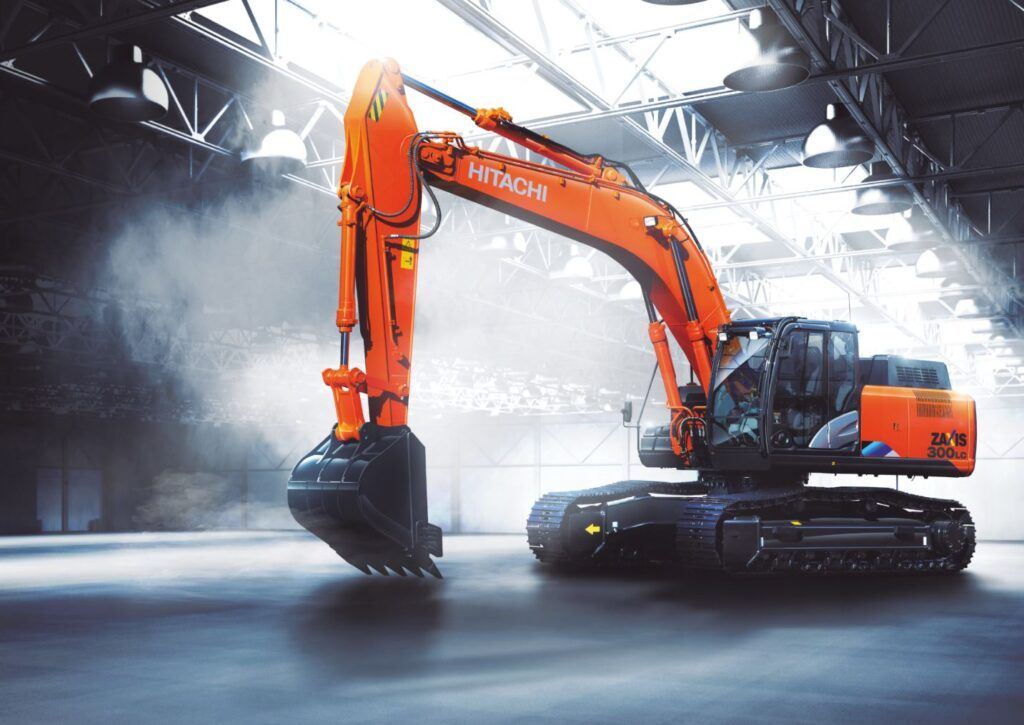
Stand FN.716
Hitachi Construction Machinery Europe is expanding its zero-emission portfolio with the unveiling of a brand-new excavator at Bauma, powered by a hydrogen combustion engine.
The new ZE300 machine, developed by KTEG (a joint venture with Kiesel Technology, announced at Bauma 2022), will be based on Hitachi’s existing ZX300 platform, and is part of the OEM’s move into larger zero-carbon equipment, adding to its existing electric range.
“The big headline for us this year is that we’re increasing the portfolio. So last Bauma, we were up to nearly 15 tonnes with our electric excavators, but now we are going to 30 tonnes with the hydrogen excavator,” Wilbert Blom, product manager for excavators at Hitachi Construction Machinery Europe tells iVT. “So we will be able to supply zero-emission solutions for wide range of applications with a wide range of machinery sizes.”
The hydrogen engine for the ZE300 comes from Deutz and has already been proven however, Blom notes, adapting it for construction equipment presented unique challenges: “It’s already been tested with stationary loads, but the challenge was to make this engine ready in terms of the software configuration for an excavator, which has permanently changing loads and which has
a highly dynamic demand towards the energy supply.”
The hydrogen excavator is still undergoing configuration work with testing expected to begin in Q3 or Q4 of 2025, making the Bauma display a genuine first look at this new machine.
Also debuting at Bauma will be the ZE150W, a 15-ton electric wheeled excavator expected to be available for purchase in mid-2026, which features innovative electric drive components. “In the past, zero emission machines just replaced diesel engine with batteries, and then you were powering the pump with it and the rest stayed the same,” says Blom. “On this one, you have electric axles. You have an electric swing. So these functions are directly powered out of the batteries.”
Hitachi will also showcase an updated version of its 13.5 tonne ZE135 electric excavator, first unveiled at Bauma 2022, with increased battery capacity (300 kilowatt hours, up from 200) and new autonomous operation capabilities, which will enable it to execute tasks like trench digging autonomously based on digital models input through a tablet or laptop.
Visitors to Hitachi’s stand can also see the KMC1200 demolition machine, which won the World Demolition Award in 2024. The machine features a configurable boom system that can reach up to 51 meters with a 3-tonne attachment or 28 meters with a 15-tonne tool.
Hitachi plans to unveil an additional surprise at the event with a concept crawler excavator model that represents ideas for the future.
Kramer 3106
Industry-first telehandler
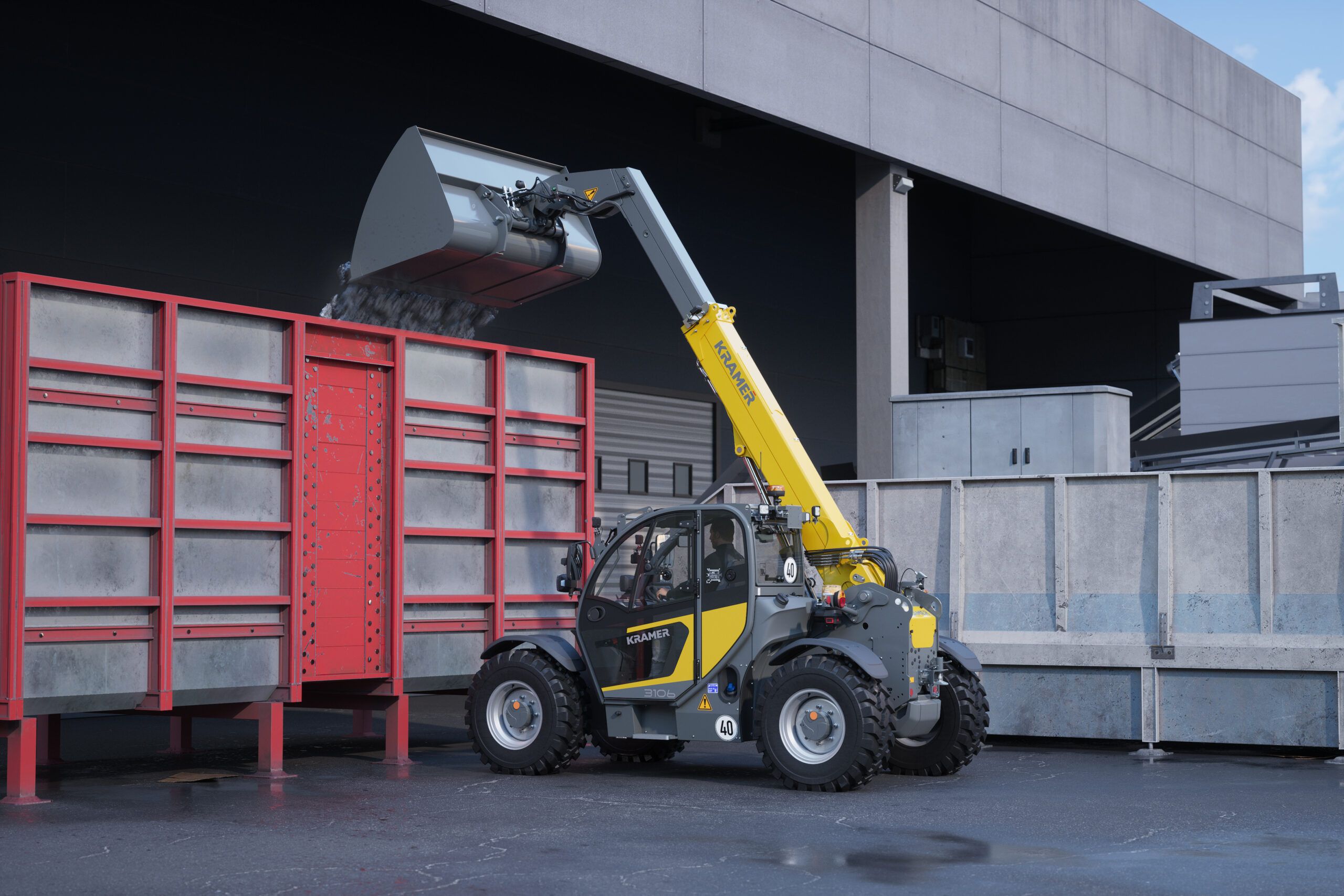
Stand FN.916
At Bauma, Kramer will be celebrating its 100th anniversary and also unveiling its new 3106 telehandler featuring an integrated automatic weighing system to enhance material handling precision.
While in recent years weighing systems have been introduced on high-end wheel loaders, Kramer believes the 3106 is the first time an integrated weighing system has been incorporated into a telehandler.
“What’s really special about the machine isn’t immediately visible in pictures,” Viktoria Sondermann, marketing team leader for Kramer, tells iVT. “You would see when you a driving on the display. It is an integrated automatic weighing system, which works completely independently of the attachment in the front, using sensors to generate the weight of the material in the shovel.”
This innovation allows operators to set specific loading targets. “You can say, ‘I want to load a container with maximum three tons,’ for example. The weighing system automatically calculates how much you’ve already put in there,” says Sondermann. “You can define a certain goal, or you can just weigh the material in the shovel. This is pretty special – it’s really new that it’s integrated in telehandlers. That’s something which is not on the market yet.”
Beyond its weighing capabilities, the 3106 impresses with robust specifications. The machine delivers a maximum payload of 3,100kg and can reach a maximum stacking height of 5.83 meters making it versatile for various construction applications. Powered by a Deutz engine producing 82kW/112hp, the telehandler combines high performance and power with agility.
Standard equipment includes a top speed of 40 km/h, a reversing fan with automatic function, and four steering modes with automatic synchronization which further enhances operational efficiency and ease of use for the operator.
Additional highlights on the 6,000m2 Bauma stand, which will be shared with sister brand sister brand Wacker Neuson, will be new 5-Series wheel loaders with enhanced cabs. A new 5045 will also be introduced with low weight (2.6t) and high power (up to 33kW) while still being transportable on a 3.5t trailer without toll charges. Kramer will also display its powerful 8-series wheel loaders.
Bauma 2025 attendees will have the opportunity to see these machines in action during live demonstrations at the Kramer stand, experiencing firsthand how a century of expertise translates into cutting-edge construction equipment solutions.
Kobelco SK90 & SK20
Battery electric excavators
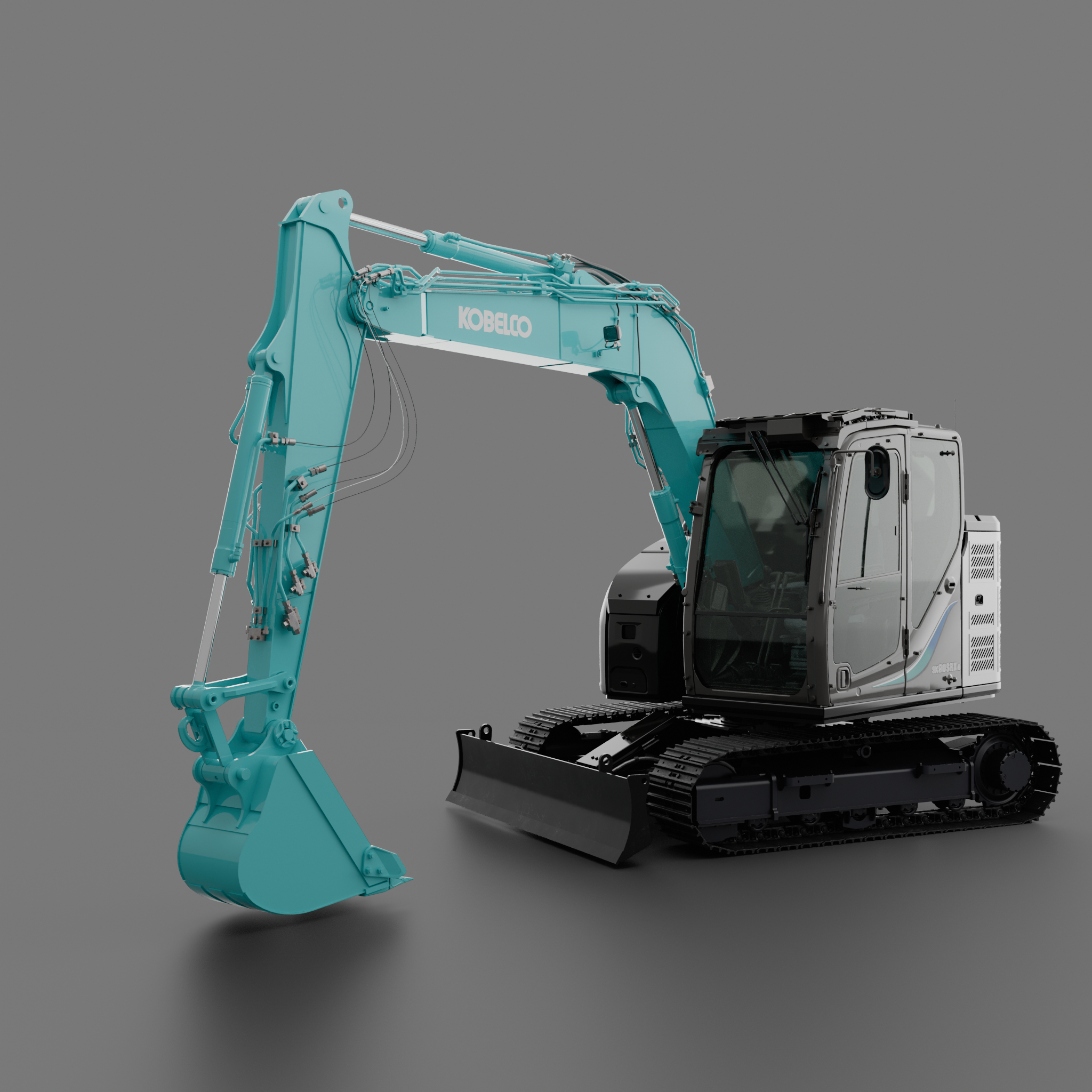
Stand FN1016/1
Kobelco Construction Machinery Europe is to debut its first-ever battery electric excavators in Munich, the SK20, based on the SK17, and the SK90, derived from the SK75 platform.
Both machines deliver six to seven hours of continuous operation on a single charge while maintaining the performance characteristics that have made their conventional counterparts popular.
“We will use Bauma as the international launch platform for our first battery-operated electric mini excavators – it’s a huge premiere for us,” says Xenia Kolijn, general manager of communications at Kobelco.
Following Bauma, Kobelco plans to deploy four machines – two of each model – to dealer rental fleets in the Netherlands for real-world testing and data collection. “The Netherlands is the largest market when it comes to zero-emission machines,” says Olivier Rasmont, general manager of product engineering at Kobelco. “We need to get some experience, get some hours. Using the dealer rental fleet makes a lot of sense.”
Although not physically present at the exhibition, Kobelco is also highlighting its hydrogen fuel-cell, 14-tonne excavator prototype through video presentations of it working in Japan. This represents another step in the company’s commitment to zero-emission construction equipment. The prototype works for four hours on a single hydrogen charge with just 10 minutes required for refilling.
Visitors to Bauma will also have the opportunity to experience Kobelco’s innovative K-DIVE remote operation system in a specially designed pavilion. This groundbreaking technology enables operators to control excavators across international borders.
“From Munich, visitors at our stand will be able to operate one machine at a site in Denmark, and at the same time operate another machine at our test site in Japan,” says Rasmont. “Customers will be able to switch from one machine to another, and we can even use the cockpit as a simulator.”
Wacker Neuson’s EZ10E and EZ26e
Electric excavators
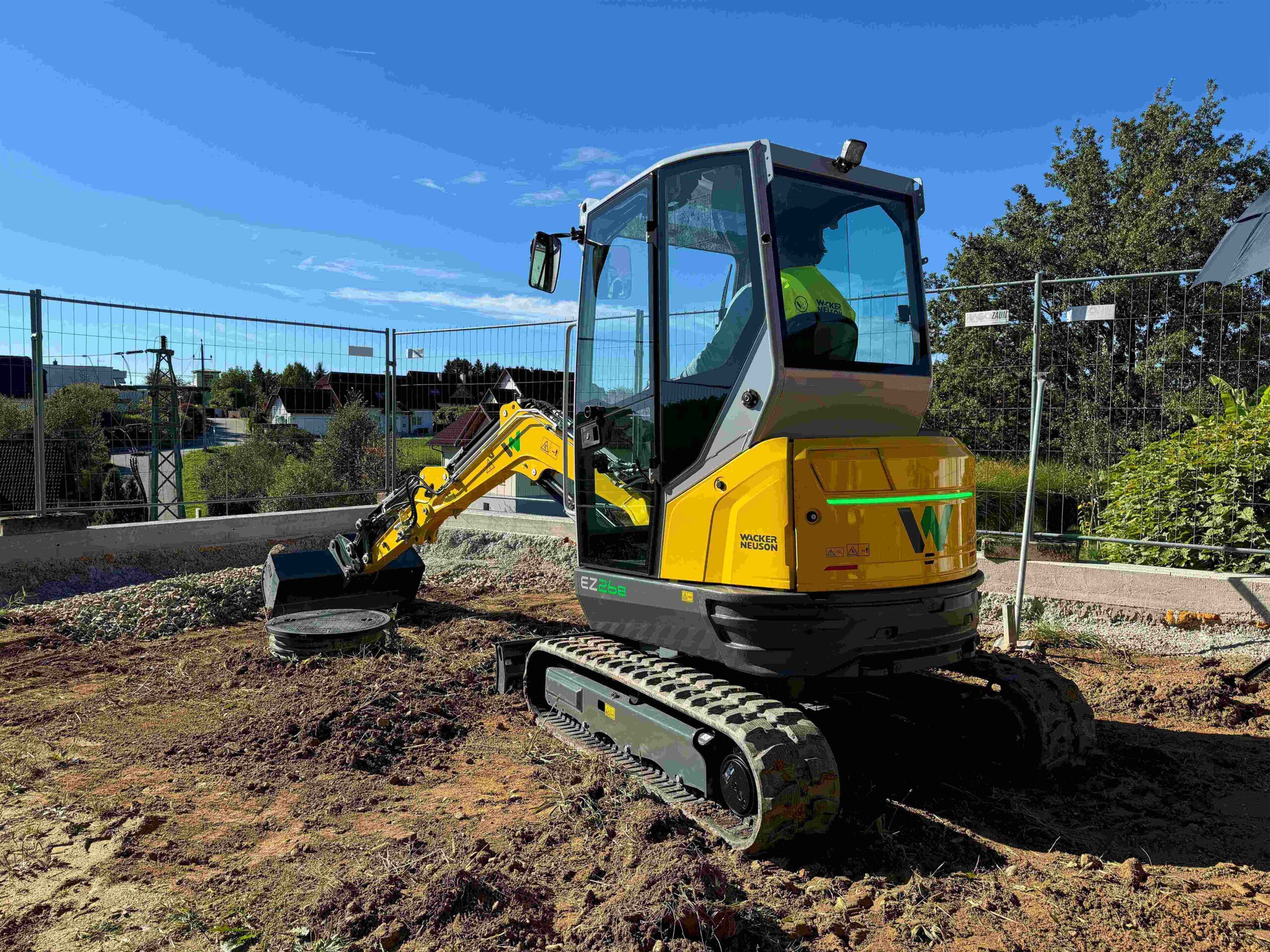
Stand FN.916
Wacker Neuson is to showcase the expansion of its zero emission portfolio in Munich with two new battery electric excavators, the 1 tonne EZ10e and the 2.6 tonne EZ26e – its largest electric excavator yet. The new additions join the existing EZ17e, meaning the OEM now offers three electric excavators in its range.
Complementing the excavators is a new electric wheel loader, the WL300e, further expanding the company’s electric wheel loader lineup. “We already have two models, and now we have three,” says Susanne Gruner, communications manager at Wacker Neuson,. “So for any application where you use one of our wheel loaders, there is now a battery version.”
To support the growing market for used electric equipment, Wacker Neuson will also introduce a certified battery check service available from spring 2025. “If you have a used machine and you want to sell it and someone doubts about the state of health of the battery, you can buy a certification,” explains Gruner. “It’s transparent, and it says how good the state of health of the battery is.”
Beyond its focus on electrification, Wacker Neuson is also introducing advanced safety and efficiency technologies for its conventional equipment. The DV60 Dual View dumper features an innovative skip change system that enables quick replacement of the skip – a first in the industry. “For our customers, it considerably widens up the range of applications you can do with only one machine,” says Gruner.
For iVT’s FULL Bauma preview read the March 2025 digital magazine online now