At Bauma, Caterpillar previewed the new Cat 775, the first next generation design of off-highway trucks for the company, planned for introduction in 2026. In Munich Caterpillar revealed that autonomous capabilities using MineStar Command for hauling are currently under development, and a release date will be announced for these at a later date.
Distinguishing it from the previous 775 models, this 65-tonne payload hauler is engineered to enable fully autonomous capabilities in the future.
“The design of the Next Gen 775 represents a significant leap forward in off-highway truck technology, offering unmatched power, efficiency and safety features. Visitors at Bauma will see our full range of technology offerings, from remote control to semi-autonomous to the future of autonomous machines in construction,” says Tony Fassino, group president of construction industries, Caterpillar.
Caterpillar is leveraging its current Autonomous Hauling Systems (AHS), Cat MineStar Command for hauling, already at work at mine sites throughout the world, and scaling the system’s processes and technology to meet the specific needs for quarry operations.
“We are using the lessons learned from working with our US-based customer, Luck Stone, where we have MineStar Command for hauling installed on four Cat 777 trucks. The shift to the aggregate industry, where we are automating fewer trucks that don’t haul material 24 hours a day, is helping transform our technology and processes to manage smaller operations,” says Denise Johnson, group president of Caterpillar resource industries, Caterpillar.
The 775 features a new frame design that helps to optimise payload weight, a refined suspension for improved ride and handling, and advanced safety features like the 360-degree surround cameras and Cat Detect radar system to deliver improved performance and safer and more comfortable operation.

“Compared to previous models, our next generation 775 off-highway truck features an industry-first frame design that reduces empty weight delivering the potential for larger payloads and lower fuel burn. Plus, its 10% more body volume and improved turning radius helps to boost productivity and performance,” says David Holthaus, senior engineer and team lead for the Cat 775, Caterpillar.
With more body volume, the truck’s new frame is optimised for weight distribution and structural efficiency. Compared to the 775G series truck, there is nearly 30% less welding to minimise the risk of cracks and improve frame life. Less internal welding and ease of frame repairability help lower costs to maintain the new 775 over an estimated 40,000-hour truck life.
According to the OEM, the 775’s redesigned suspension boasts a lower centre of gravity. The machine has shown to deliver better handling than previous designs, and an updated turning radius enhances on-site manoeuvrability. Improving service life, the truck experiences less bouncing on the tires and driveline, and the operator feels less vibration and energy feedback into the truck.
The truck is powered by the 615kW (825hp) Cat C27 engine and comes in different emissions configurations to meet different global regulations. The US EPA Tier 4 Final/Stage V version displayed at Bauma offers better fuel efficiency than previous models, with advanced electronic powertrain controls that deliver faster cycles and reduced road maintenance.
The truck’s enhanced ride and handling allow for higher speeds on curves and driving in higher gears, which directly reduces fuel consumption during the cycle.
Caterpillar says that the new cab is designed for efficiency and equipped with features to automate functions. The large windows give the operator visibility to the work area and surroundings. Automatic cab temperature controls and the Cat next generation deluxe seat is designed to help to improve operator comfort.
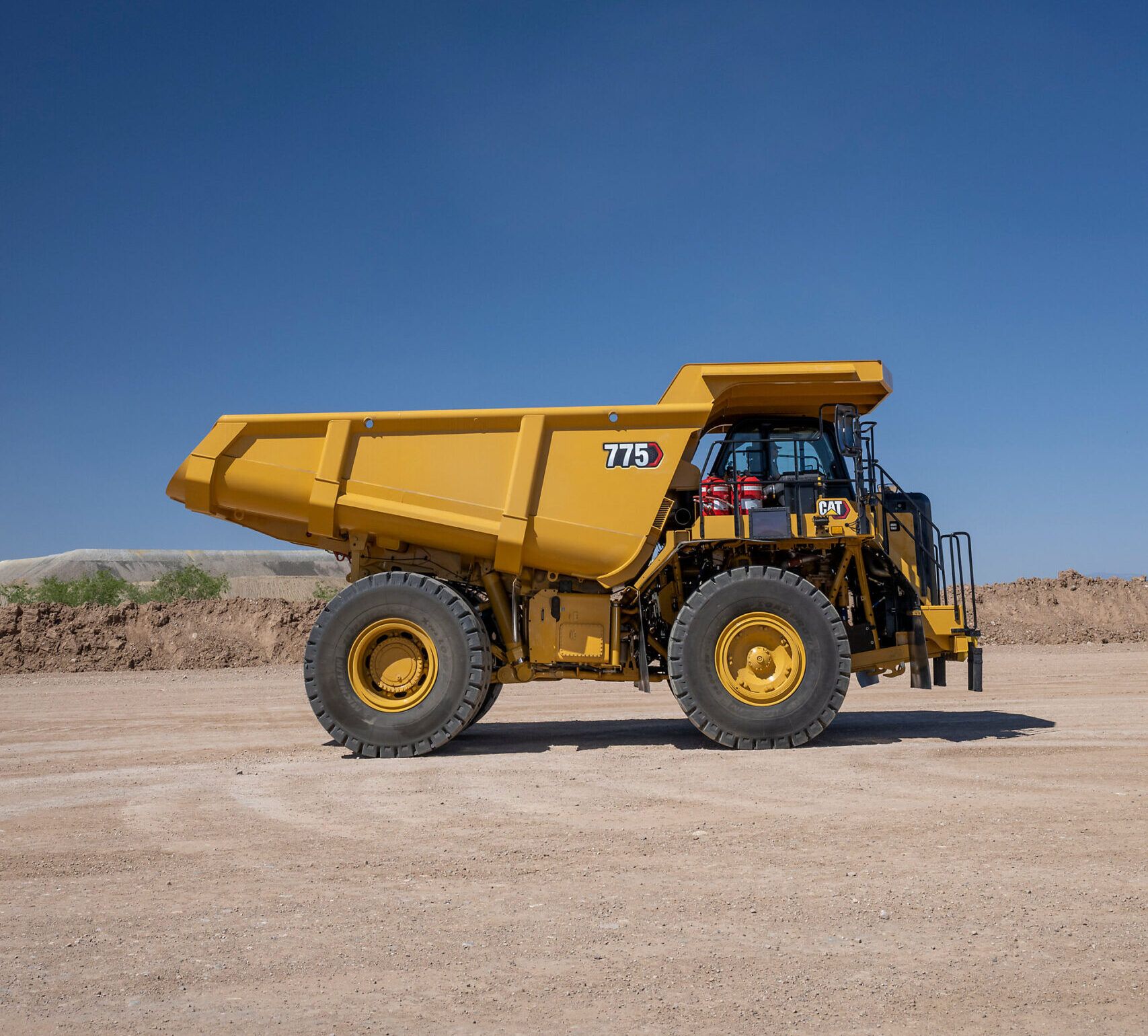
Its 360-degree surround cameras with object detection alerts operators to hazards within the immediate vicinity, making it easier to safely operate the new 775. Cat Detect combines radar and camera systems to automatically detect hazards within critical areas around the truck – primarily the front, rear and turning radius on each side.
Multiple key maintenance and service contributors have been reduced with the new truck design. The next generation of enhanced serviceability incorporates extended-interval filters with ground-level access, ground-level lockout features and a serviceable suspension. Its design is fire suppression ready to simplify system installation.
The ability to access and analyse accurate real-time data enables faster diagnostics and enhances the ability to predict and prevent machine failure. New for the 775, remote flash and troubleshooting capabilities help to boost truck availability. Remote flash instantly provides access to the latest software updates and enables the updates to be scheduled and executed at a time that doesn’t interrupt the production schedule. Remote Troubleshoot enables the dealer to perform diagnostics remotely while the truck is still in operation.
Images courtesy of Caterpillar