Bobcat has confirmed that the focus of its R&D approach will be in improving connectivity, performance, sustainability and safety.
Thanks to the acquisition of sister company, Doosan Industrial Vehicle, which manufactured a leading line of forklift trucks and warehouse equipment, Bobcat can now offer its customers an even more complete package of material handling solutions.
The rebranded Doosan equipment builds on the existing compact loaders and telehandlers from Bobcat, which can be equipped with attachments such as buckets, grabs, bale clamps, dump hoppers and pallet forks, so they can be used in many industries for material handling and logistics work.
The forklift range alone consists of dozens of models, including diesel forklifts with a lifting capacity of 2 to 16 tonne; LPG forklift trucks with a lifting capacity of 1.5 to 7 tonne and electric forklift trucks with a lifting capacity of 1.5 to 10 tonne.
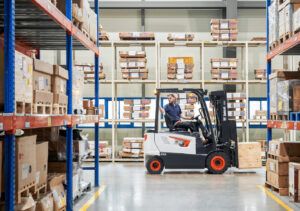
Product development has led to a number of innovations at Bobcat. These include the electric machines that Bobcat has presented to the market in recent years, with the E10e and E19e mini-excavators now available for purchase in Europe, the fully electric T7X track loader in a limited launch in North America and the S7X skid-steer loader, as well as the recently revealed TL25.60e electric telehandler concept machines.
In addition, the MaxControl remote control for machines and MachineIQ for remote monitoring of machines have also been introduced. With the latter tool, the status and performance of machines can be monitored and optimised.
Bobcat has recently showcased innovations for logistics and material handling. These include prototypes of the B18NT electric forklift truck with 3 wheels and a lithium battery and the B30X-7 Plus hydrogen forklift truck.
An important expansion now on the market is the new NXE series of electric forklift trucks with 4-wheel drive. The series consists of forklift trucks with a capacity of 6 to 10 tonne, which are suitable for heavy applications in container transport, machine construction and industry. These zero-emission machines can work an entire day on a battery charge and are of course very suitable for work in factories and warehouses. The machines offer excellent visibility, comfort and features as standard that make operation easier.
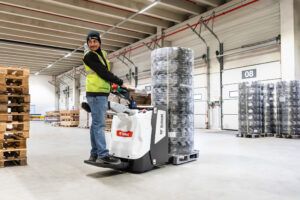
Data and connectivity
According to Vijayshekhar Nerva who is responsible for innovation at Bobcat EMEA, the company maintains four key principles for R&D. The first is connectivity. Companies have access to enormous amounts of data that are important for their activities and that data must be available in real time and in the machines as well. It also concerns the performance and productivity of machines. They must function optimally when carrying out work. The third principle is sustainability. This not only concerns emissions, but also the use of sustainable, robust materials in the production of machines and ease of maintenance, so that machines last longer.
 Safety and efficiency
At Bobcat’s recent Demo Days event for the EMEA region, visitors were able to see the very latest developments in the fourth segment of safety and efficiency. They included new operator presence technology that leverages a 3D time-of-flight (ToF) camera to monitor users’ movements and the cab environment, enhancing safety by preventing unintended machine actions. The pedestrian detection camera uses AI-enabled processing capabilities to differentiate between humans and surroundings, reducing unnecessary operator alerts.
Bobcat’s transparent OLED (T-OLED) screen technology, developed with LG and BSI Research, enables operators to access various functionalities without taking their eyes off the worksite. This technology facilitates advanced applications like real-time virtual reality (VR) simulations for utility line mapping.