Human-machine interfaces (HMIs) must adapt rapidly to evermore complex vehicle functions while remaining clear and intuitive. Expert designers in the field discuss the challenges and reveal some of their current and proposed solutions
As human-machine interfaces (HMIs) evolve, a balance must be struck between technological advancement and practical usability – just because a control panel is state-of-the-art doesn’t mean it automatically creates the most intuitive system. Instead, OEM designers must weigh up the competing demands of innovation, safety, and operator effectiveness.
The off-highway industrial vehicle sector is seeing a significant trend toward larger screen sizes, driven by both the increasing affordability and the growing need to present more complex machine information.
“Alongside larger screens, there’s a need for larger graphics which offer a clear view of relevant details,” says Herman Oberoi, senior portfolio manager for displays at Danfoss Power Solutions, explains “Gauges are a good example where readability is important.”
Larger screens also mean there is an opportunity to cut down on the number of displays in a cab, with ‘screen clutter’ a familiar problem for designers and operators alike. “Space management in new cabin designs is another influence,” says Oberoi. “There is a need to show consolidated, yet more detailed, information on bigger screens at one glance.”
Cutting down on clutter isn’t the only benefit of screen consolidation, it also creates the opportunity to create better control systems. “In a modern excavator, you could easily have four different displays in the cabin, and even if you have great UI or UX in one display, you still have four displays,” says Petri Moisio, CEO of Novatron, a Finnish technology company specialising in automation and machine control for construction.
Using just one screen creates an opportunity to standardise UX, which can create challenges for specialised functions. “Off-highway tools are not legislated or standardized as much as commercial devices like cars,” says Moisio. “Every single car has the same symbol for the fuel tank and fuel levels and turning signals. But if you look at off-highway machine control systems, they are quite heavily regionalized.”
While pushing for standardisation designers need to remain alive to the risk of alienating operators with changes they don’t understand, even ones that are seemingly insignificant. “Our founder made a second-generation device with two buttons instead of one,” says Moisio. “The feedback from customers was that this product was awful – ‘I don’t know how to use it,’ they said. ‘There are two buttons instead of one’.”
“In a modern excavator, you could easily have four different displays in the cabin, and even if you have great UI or UX in one display, you still have four displays”
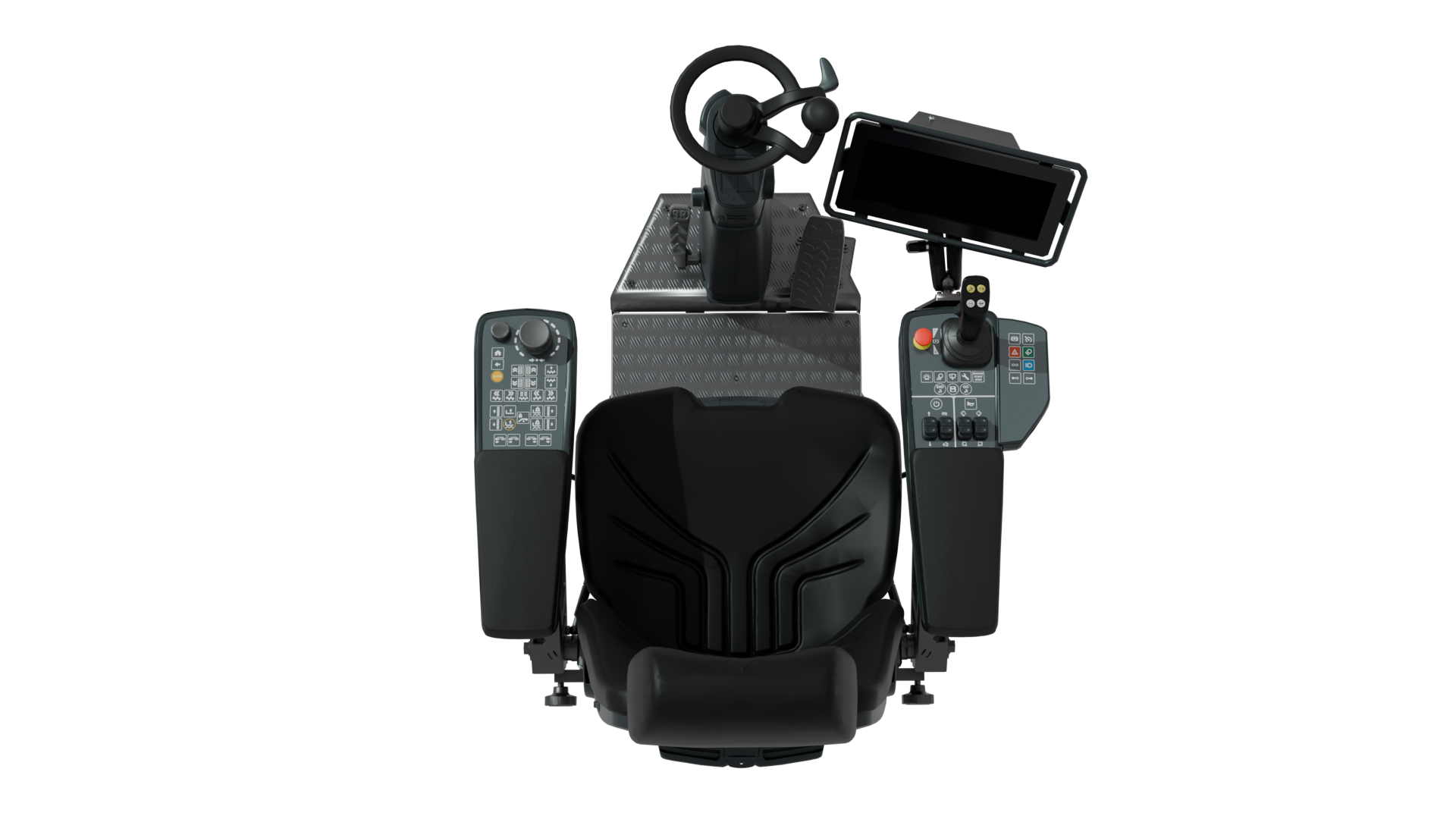
OEM HMI
Road-building machine OEM, Dynapac had the reduction of screen clutter and also the enhancement of user experience very much in mind when it developed a completely new HMI centred around its PaveOS for its new range of SD/XD pavers, which will be launched at Bauma Munich.
Integral to the HMI design is two, 12in+ widescreen displays, which enable full touch interaction while still maintaining compatibility with traditional controllers. Each screen features high peak brightness that can be dimmed for low-light operations.
Importantly, Dynapac’s PaveOS has an open-interface architecture that means that other third-party applications can be integrated. Split-screen technology means part of each widescreen display is always reserved for critical machine data, while the other section is fully customisable, eliminating the need to install additional screens.
“The framework is designed so you never lose focus on your paving job,” says Sönke Demuth head of global product management for the paving division at Dynapac. “One part of the screen is always reserved for application data, while the other part can be used for settings, assistant systems, bird view camera systems, or whatever else you need.”
Widgets, quick links and machine functions can be freely assigned on the home screen according to personal preferences. “During our research, we noticed that people don’t use our machines in the same way,” says Demuth. “So we created widgets on the display that the operator can choose, and interaction points can be customized according to individual user preferences.”
Moreover, all data can easily be offloaded from PaveOS for analysis. “The data can be easily accessed, shared, and used to optimise workflows. It’s your data, and we offer you full control over it,” says Demuth.
This new interface represents a complete overhaul of Dynapac’s previous system, which dated back to 2011. “We needed to break out of our old environment,” says Demuth. “So we started again from scratch. We wanted to rethink it in-depth and create something new that is prepared for the future.”
The new Dynapac HMI isn’t only about screens: all the XD series controls are ergonomically integrated into the driver’s seat, ensuring maximum comfort and enhanced forward visibility.
While redesigning systems from scratch is one way to address concerns over multiple screens, in the short to medium term and to meet the challenges of already embedded HMI, MTA has developed and put on the market a system aimed at agricultural machinery, called AgriSic. It is an intelligent central unit, able to drive different displays, enhancing safety and cost efficiency. “Agrisic allows for the integration of compact and small displays without compromising functionality,” says Ivan Dal Santo, electronic business unit director for MTA “With specialized agriculture functionalities seamlessly integrated, it empowers vehicles to manage complex services and functions simultaneously. Leveraging the latest connectivity technologies, the system guarantees efficiency, reliability, and durability while delivering top-tier reception.”
“One part of the screen is always reserved for application data, while the other part can be used for settings, assistant systems, bird view camera systems, or whatever else you need”
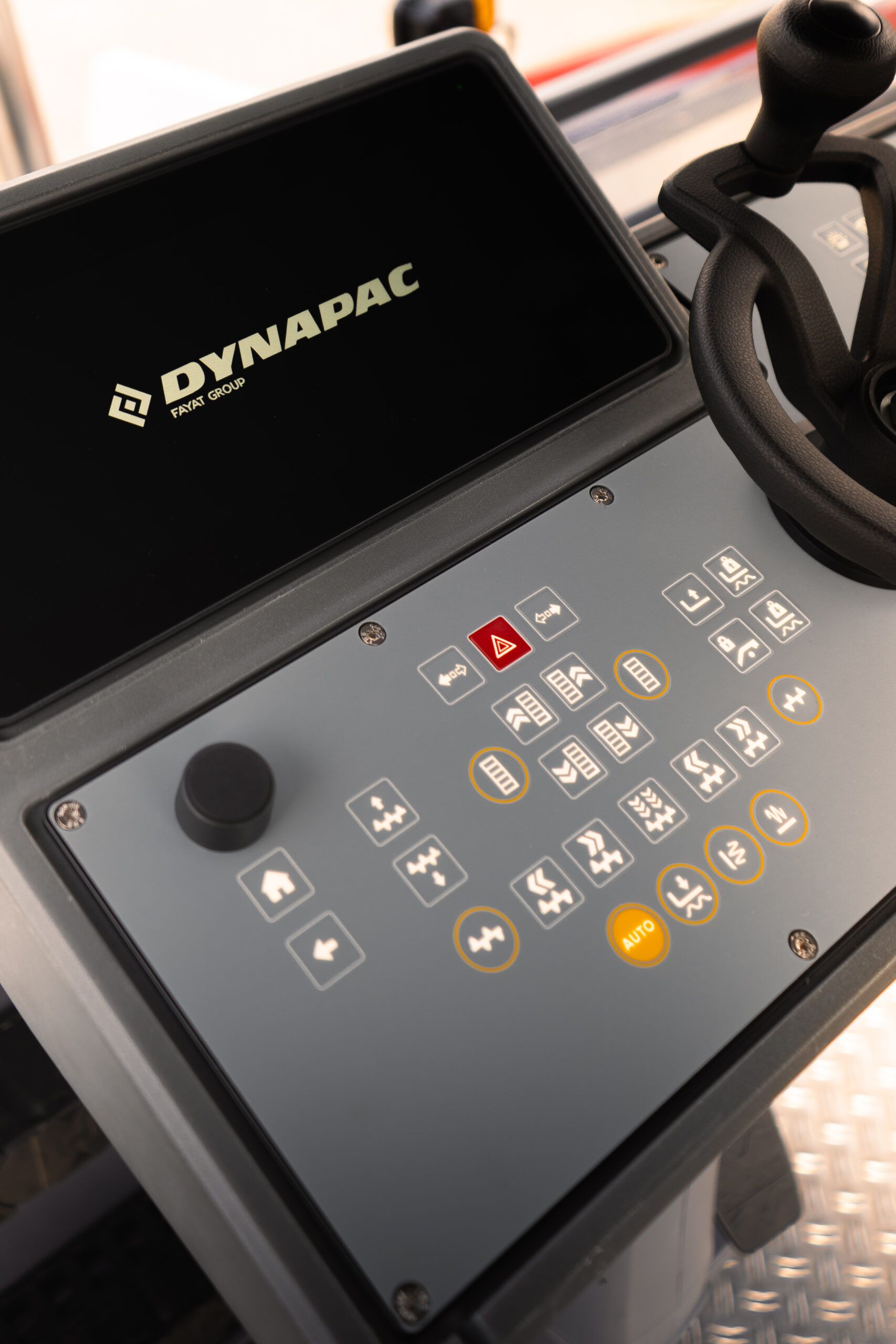
Controlling autonomy
As the off-highway industry moves toward greater automation, human oversight remains crucial to most systems, meaning HMI must adapt to provide not only an effective method of control, but also a way for users to oversee operations.
“Even during autonomous operations there are a number of different safety considerations that require an operator either in the cabin of the machine or nearby,” says Oberoi. “Both of these cases need an HMI cluster to monitor and oversee the machine.”
It is clear, therefore, that the trend toward automation is beginning to change the very nature of operator roles. “Sometimes autonomous machines need assistance from the operators,” says Moisio. “But the function of the operator will be completely different – the operator’s purpose might be mainly to supervise the autonomous machine.”
As machines become increasingly automated a whole new HMI challenge is emerging in maintaining operator engagement. “Humans need interesting input,” says Amber Case, founder of the Calm Tech Institute, which looks at the best ways to create human-centric HMI. “How do you give people that mental stimulation, so that they make fewer mistakes and they are not just babysitting
a screen all day?”
Case advocates for what she terms “pass-through interfaces” – technologies that allow users to focus on their task in hand rather than the tool being used to do it. “A hammer becomes invisible when you use it. A car, if designed well, becomes invisible when you drive it.”
Therefore, the challenge for designers of HMIs for autonomous vehicles is to create ways in which humans can focus on the critical path itself, possibly across multiple machines, rather than simply
watching the machine doing each stage of its job. This could create vehicle systems that are an extension of human will, rather than basic single-function automatons.
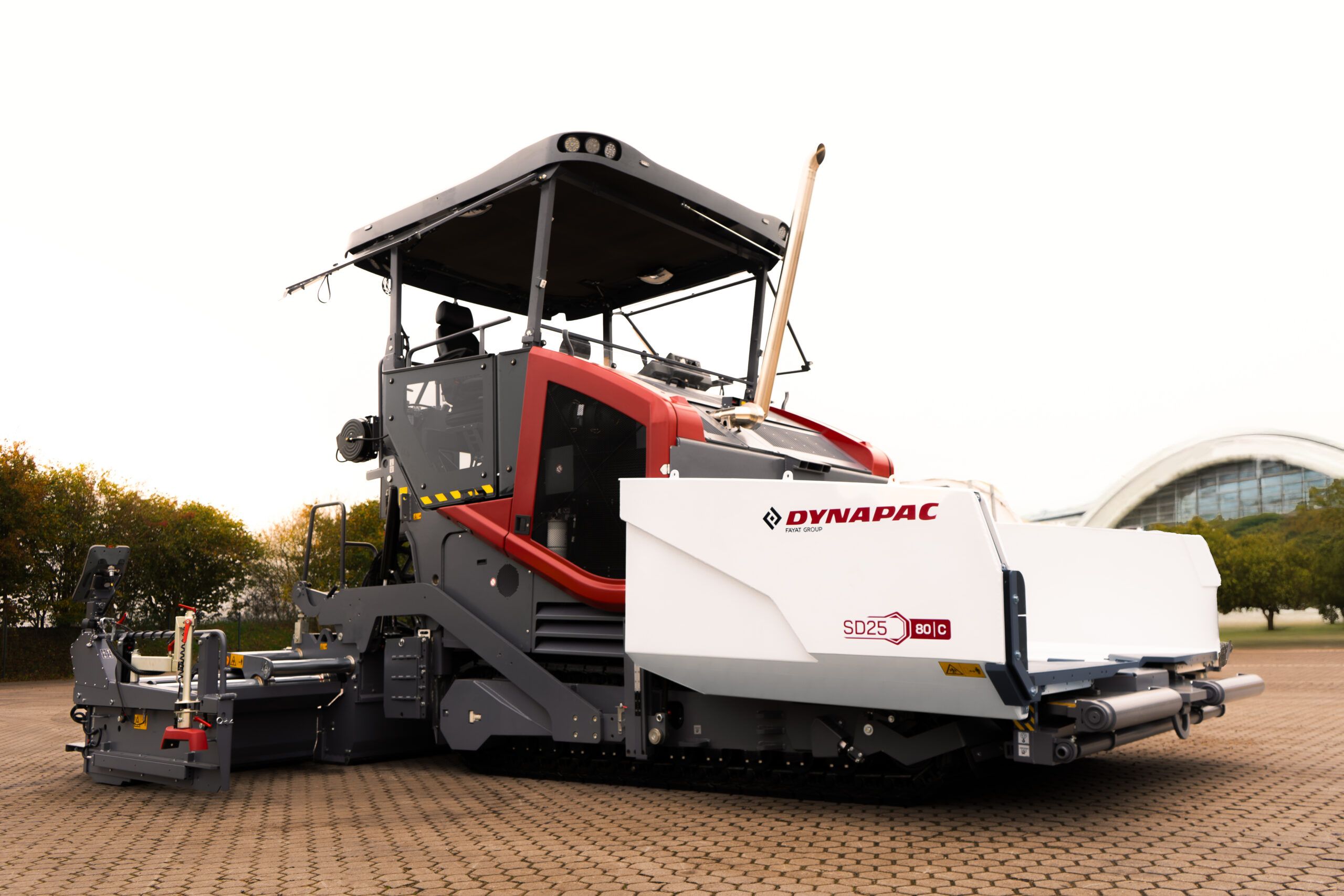
Even in the world of artificial intelligence human oversight is likely to remain critical. “The world of autonomous functionality could certainly embrace AI, especially where a machine can perform a task precisely,” says Mohamed Abd El Salam, senior portfolio manager for IoT and Connectivity at Danfoss Power Solutions. “As for whether AI can be relied upon to make critical operation decisions, this might need to be pushed back to the operator as a recommendation via HMIs – it may never be executed in a fully autonomous way.”
“How do you give people mental stimulation, so they make fewer mistakes and are not just babysitting a screen all day?”
Navigating ahead
The future of HMI in industrial vehicles lies in finding the right balance between technological advancement and practical usability. This balance must account for regional variations in operator preferences and regulations, safety requirements, and the changing nature of operator roles.
Some markets and sectors retain a strong preference for physical controls over screens. “We see some inclinations to stick with physical buttons, as well as CAN keypads on the armrest in some regions and for certain applications where safety concerns are higher,” says Oberoi, of Danfoss Power Solutions.
But screens are more adaptable to future technology than dials and switches. “The HMI must be prepared for what’s coming in the future,” says Diogo Mendonca, product manager for microcontrollers at German electronics giant Infineon. “This is the complex challenge we need to face.”
Success in the evolution of HMIs requires careful consideration of the human factors that are at play, the technological capabilities that must be represented and the safety requirements. The goal is not simply to add more features or larger displays, but to create interfaces that enhance rather than complicate the operator’s ability to perform their core tasks effectively.
This article first appeared in the March issue of iVT