Here is iVT’s full, in-depth case study of the largest combine harvester in the world – New Holland’s CR11 – including a detailed look at the all-new technology
New Holland first introduced its brand new, completely redeveloped CR11 combine harvester to the public at last November’s Agritechnica, in the process landing a Gold Award for Innovation. It’s main selling point to customers was that being boosted with cutting edge technology, the machine can harvest crops with greater efficiency and productivity, while reducing grain loss and harvesting costs. It also happens to be regarded as the world’s largest combine.
Taking the legacy of the company’s flagship CR line – notably topped by the CR10.90, world record holder for the most wheat harvested in eight hours – the new CR11 was designed, and is being produced, at New Holland’s Centre of Harvesting Excellence in Zedelgem, Belgium.
Highest productivity on the market
Next year marks the 50th anniversary of the New Holland Twin Rotor technology, and the new CR11 highlights the advantage of the Twin Rotor concept that revolutionised combine harvesting. It’s thanks to the Twin Rotor technology that the new CR can offer the highest productivity at lowest grain crackage on the market.
“The CR11 is a completely new combine constructed using over 8,000 newly developed parts, which equates to over 90% of the parts used,” says Geert Nerinckx, New Holland’s CR11 global product manager. “This is a bigger combine and is much more productive than many on the market. Its main goal is to reduce the total cost of harvest for our customers.”
Looking closely at the machine, and starting with productivity, the feeder channel has been made wider to allow more material through. It has bigger rotors that are 50% longer, and this allows the machine to feed directly into the resident system.
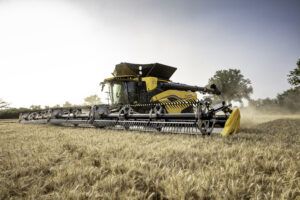
Improved bottom line
More productivity, close to zero grain losses, better and more efficient residue management and a significant reduction in downtime are the four pillars the CR11 was built on – and with a higher overall objective to reduce the total cost of harvesting to improve the farmer’s bottom line profitability.
The CR11 is powered by a bigger engine, the Cursor six-cylinder, 16 litre 775hp C16 engine by FPT Industrial. The combine’s grain tank capacity has also been increased
to 20,000 litres.
“The grain download rate has been increased to 210 litres per second which means the bigger grain tank can be emptied in less than 100 seconds,” says Nerinckx.
Industry first
With a design goal of zero loss, the New Holland engineers developed the double cleaning shoe. The new Twin Clean cleaning shoe comes with two cleaning systems behind each other, with two upper sieves, two lower sieves, two clean grain augers and two sets of pressure sensors to measure cleaning shoe load.
As an industry first, the new Twin Clean system is fully automated to guarantee even cross distribution of the cleaning shoe, for maximum capacity, but still with grain loss levels close to zero.
“When you have such high capacity of grain, it needs to be cleaned efficiently, while making sure there is no grain loss,” says Nerinckx. “We gave our engineers the task of designing a cleaning shoe with zero grain loss and they came very close to that goal.
“We call it Twin Clean, which means it has two cleaning systems in one cleaning shoe. There is a wider and longer cleaning pan which is followed by two cleaning systems, and is all fully automated. It is all part of the IntelliSense information system of the combine, and continuously measures cleaning shoe load, left, right and after, using sensors. If it detects any anomalies left or right, it will correct the distribution automatically.”
Meeting future demands
New Holland says it has designed the new CR11 in anticipation of the way in which future harvesting demands will continue to evolve. It also factored in feedback from customers seeking greater capacity, lower grain losses and maximum protection of the grain quality.
Recognising how higher yielding crops and unpredictable weather can affect both one season’s crop and the next, New Holland engineers aimed to design a machine that can play
its full part in delivering maximum productivity, and clear fields quickly to ensure quality is protected and the following year’s crop establishment can take place in good time and in good conditions.
“We are working with 15m headers but have also tested 18m headers in Australia,” says Nerinckx. “Some contractors will wish to spread the residue material over the full width of cutting, therefore we have a completely new automated resident system to do that.”
The CR11 comes with Intellispread and two radars, one on the left and one on the right of the combine. Radar beams show the operator exactly where the straw particles are landing in the field, even through the dust clouds generated by the machine.”
“Its main goal is to reduce the total cost of harvest for our customers”
Chop and spread
The completely new residue management system features a brand-new chopper and chaff spreader system, designed to ensure the best chop quality and even residue spreading over up to 60ft cutting width.
The Intellispread radar system, winner of a 2022 Agritechnica Innovation Silver Medal, automates the spreading control to ensure full and even residue coverage behind the combine, regardless of wind effects, crop type or moisture conditions.
“On the driveline, the entire cropflow channel is wider, but the transport width is still the same,” says Nerinckx. “We were able to achieve that by putting some of the drives inside the channel. For example, we are using the left rotor for the driveshaft of the Dynamic Feed Roll. That’s means that the entire DFR driveline goes away and you can widen the cropflow channel because you are driving the DFR with your rotor.”
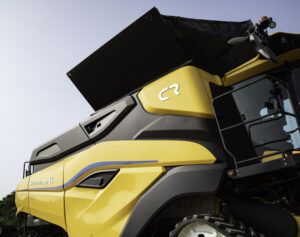
Reduced downtime
The engineers also came up with a new automated unblocking procedure, designed to reduce machine downtime. While the new CR11 combine is ready to be pushed for maximum throughput, New Holland recognises that it is impossible to completely eliminate any risk of plugging the machine with straw. In the unlikely event of operator error causing a blockage in the combine, the automatic system to unblock will kick in and guide the operator through an unplugging procedure in a way that clears the combine in minutes rather than hours, without requiring the operator to exit the cab or perform any physical effort.
No fear of blocking
Because it significantly reduces downtime caused by such a scenario, the automated reverser helps and encourages the operator to exploit the combine’s full capacity potential without fear of blocking. In addition, this feature increases safety while clearing a blockage, because no person is leaving the cab during the automated unplugging process.
Fewer drive components
Downtime prevention is further aided by the combine’s revised driveline simplicity with as much as 25% fewer drive components and with the elimination of all chain drives.
“Another benefit of this combine is that we no longer have any drive chains, only belts, shafts and CVT drives,” says Nerinckx. “With 25% fewer drives, the benefit is the operator can unblock the combine from inside the cab.
“Every combine driver who has blocked the machine and knows it can take hours to clear it out. With this system, if a blockage occurs, the combine itself will search for the blocked material, clear the blockage, pull the material through, and within five to 10 minutes normal harvest operations can proceed again, with the operator never leaving the cab.”
Best seat in the house
Inside the cab of the CR11, New Holland has mounted the new Intelliview 12 display and IntelliSteer guidance system, together with other essential precision farming functions such as telematics and remote screen viewing, for ease of use.
Also, NutriSense comes with a NIR sensor that monitors crop quality via the use of near infra-red light to analyse nutrients like protein, starch and oil contents, plus moisture levels, and can create maps of these for further agronomic analysis.
“The cab also comes with a bunch of upgrades,” says Nerinckx. “It has a striking new design, new seat and a brand new console. A new console was necessary as we have 10 new controls, that were manual outside the cab, and are now inside the cab as remote controls. Remote controls gives comfort to the operator and also reduces the downtime of the machine, as there is no need to stop and go outside to change the manual controls. These remote controls in the cab can be automated.”
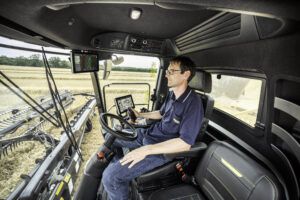
The right track
Visible upgrades on the new CR11 combine include the new 15m (50ft) draper header manufactured by MacDon for New Holland.
Recognising the trends for reduced ground compaction in combination with transport width regulations, the CR11 offers a range of wider tracks and bigger tyres.
The machine at Agritechnica was fitted with tyres from Michelin, the Michelin Cerexbib 2, size 900/65R46 with a diameter of 2.32m, which are the result of a co-development between New Holland and Michelin.
Next-level tyre size
New Holland says this is the first time that this next level of tyre size has been introduced on a combine of any type, and the longer tyre footprint and increased traction provide a reduced ground compaction with no precedents in harvesting.
Visually, the manufacturer believes that close collaboration between industrial design and engineering teams, together with product specialists and brand marketing, created such a new, impressionable design that focuses on customer needs as well as aesthetic sensibilities.
The end result is an iconic, refreshed design that is stylish yet timeless. The flow of the harvest is underlined on the exterior panels by the dynamic blue feature that runs across the sleek body through the various functions.
This article also appears in the June/July 2024 edition of iVT International