Multiple OEMs have publicly committed to hydrogen combustion engines for future mid-size and heavy equipment. But are they market-ready and is the market ready for them?
While battery technology and electrification are making market progress as practical alternative power options for compact construction and agriculture vehicles, the majority of manufacturers would appear convinced hydrogen-fuelled adaptations of conventional engine bases offer the best blend of attributes for heavier machines and higher power demands. But although recent years have seen plenty of prototype unveilings at trade exhibitions and press events, full market availability and broad industry adoption of such power technology would appear still some way off.
While the framework has long been in place to supply, store and dispense liquid fuels and electricity, development of the necessary technology and infrastructure to do the same with hydrogen is perhaps a good few steps behind that of the machines that can use the fuel. It’s this that would appear to be what the market needs to spark demand for hydrogen-fuelled farm and construction equipment. But is it that simple? What stage are manufacturers at with their machines?
Refuelling development
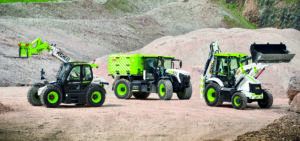
While initially trialling hydrogen fuel cell technology to power a prototype 360-degree excavator, JCB latterly shifted its hydrogen focus to less complex and more responsive hydrogen-fuelled internal combustion engines, with the added benefits of less cooling demand and much-reduced weight over a battery-based hydrogen fuel cell unit. Well-established in its commitment to hydrogen engine power for its larger vehicles, having publicly demonstrated backhoe loader and construction-spec telehandler working prototypes, JCB has gone some way to also develop the necessary technology to support hydrogen-engined vehicles.
“Our hydrogen engine development is not a conversion, but new combustion technology,” says Ryan Ballard, engineering director for powertrain at JCB, speaking about the company’s four-cylinder engine that features in those working prototypes, and which was given its standalone world debut at last year’s ConExpo.
“Because of the different characteristics of a gas fuel compared to a liquid one, it requires a completely different low-pressure, low-temperature combustion process. We have developed a specific oil and additive pack that, at low initial engine temperatures, traps the water produced as a combustion by-product. As the engine warms to operating temperature, that water then dissipates.
“We’ve also developed a high-efficiency turbocharger that forces much more air into the engine than a standard unit, helping maximise hydrogen combustion efficiency.”
But while the principle of the engine has now been established for some time, the infrastructure required to support it and others like it – and the practicalities of fuelling a machine powered by the unit – are something JCB has only addressed more recently, with the unveiling of its mobile hydrogen refueller.
Based on the stretched platform of one of its Fastrac 4000-series tractors, the refueller is designed to transfer hydrogen fuel between on-site bulk storage and hydrogen-powered machines. It features standard nozzle technology for hydrogen fuel delivery from refueller to machine, and refuelling time is comparable with that required for refilling with diesel, whilst the unit’s capacity gives it the ability to provide up to 16 refills before the unit itself needs replenishing. The company suggests this system will suit most users in that it mirrors how they already manage the refuelling requirements of diesel-powered machines.
Manitou prototypes
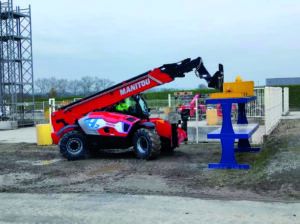
Among other handling equipment makers, Manitou Group says that, by 2030, low-emissions products – electric plus hydrogen – will represent 43% of its product line. The firm has opened dedicated facilities for hydrogen-powered machine development and has a hydrogen-powered prototype telehandler – based on an existing 18m-reach construction machine – in development, with tests ongoing to guarantee range and reliability in real-life conditions, plus component durability. While this initial prototype uses fuel cell technology, Manitou says it will ultimately select the hydrogen power system best suited to its customers’ needs.
“We are studying all the hydrogen-related technologies based on what users need,” says Michel Denis, president and CEO of Manitou. “This current prototype is only the first step – a second rotating telehandler prototype will be developed in the coming months.”
To develop a solution suited to full industrialisation, support from public authorities to develop an emerging ecosystem is critical, emphasises Julien Waechter, Manitou Group vice-president of R&D. “The green hydrogen sector is gradually becoming more established with the entry of more players,” he says. “All of the aid mechanisms proposed by the different governments will encourage the transition to hydrogen, and will speed up the development of the distribution network and ultimately the reduction in the usage costs of our machines using this energy. Our aim is to have a 100% hydrogen-powered telehandler on the market by 2026.”
While JCB has arguably taken a sector lead in hydrogen-engined off-highway vehicle development, other multinational OEMs are also committing serious R&D money to hydrogen engine vehicles. Elsewhere in the construction sector, Liebherr continues to work on its H964 four-cylinder and H966 six-cylinder engines, the latter having been developed in conjunction with the firm’s R 9XX H2 excavator. Series production of its hydrogen engines is expected to begin in 2025.
Injection challenges
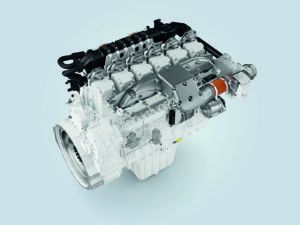
With higher injection pressure and the exposure to combustion pressures and temperatures raising requirements on injector tightness and durability, Liebherr continues to test its H2 fuel injectors and complete injection systems for safe and accurate direct injection operation. Using a system-oriented approach to hydrogen injection, the aim is to match the performance of an H2 DI engine to that of a diesel engine, requiring any system to be capable of ensuring high flow rates.
Due to the low density of hydrogen gas, an injector needs large valve cross-sections. To enable precise control of small quantities, the system pressure must be regulated with pinpoint accuracy, points out Liebherr. In the firm’s hydrogen injection system, this is achieved via a gas volume control valve, working alongside other pressure- and flow-regulating components to create a system-oriented approach to hydrogen injection. In addition to its direct injection activities, Liebherr says it is working in parallel on intake manifold injection components to meet different engine requirements.
The company has been working with Mahle Powertrain to incorporate the latter’s prechamber jet ignition system (MJI), with engine tests showing that its use can combust the hydrogen/air mix at a high compression ratio, maximising the process’s stability and efficiency and enhancing green hydrogen’s suitability for heavy-duty and off-road applications.
“The challenge is to stop engine knocking and premature ignition without reducing the compression ratio and thus efficiency and performance yield,” says Mike Bunce, head of research for Mahle Powertrain US. “In order to achieve stable operation with a high compression ratio whilst avoiding engine knock and pre-ignition, hydrogen engines must be operated with a large amount of air. The energy from a conventional spark plug is insufficient to ignite such a mixture. Our Jet Ignition solves the problem by burning a small amount of an ignitable mixture in a prechamber. The resulting gas plasma is passed through small openings into the main combustion chamber and, due to its high energy content, rapidly and evenly ignites the main gas mixture. Tests with Liebherr’s H966 and H964 engines have delivered excellent results in terms of combustion speed, performance and emissions.”
Indian push
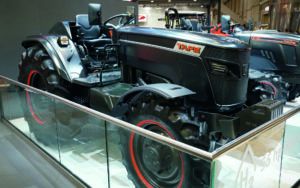
In terms of agricultural vehicles, Indian tractor giant TAFE used Agritechnica 2023 to mark its broader push into the full western European farm tractor market by unveiling to attendees both battery- and hydrogen-powered developments.
Ravindran Vijayakumar, the company’s chief engineer, has revealed that the modified Simpson engine in the tractor produces 55hp/41kW from its three cylinders, but has also stated that little further information will be available until further development had been carried out.
“This is a fully-working prototype, and we know we can carry sufficient fuel for long working periods, with our design engineers having incorporated considerable fuel storage capability into the tractor through purpose-designed tanks behind the operator’s seat and beneath the platform floor,” says Vijayakumar. “That will be one of the most crucial aspects of machine acceptance. A tractor with this fuel type would be targeted initially at markets with the infrastructure to support it, which is why we are making a concerted push into western Europe.”
In terms of firms focused solely on manufacturing engines for OEMs, Antonio Leitao, vice-president of off-highway engine business at Cummins, also used Agritechnica to underline the company’s commitment to hydrogen as a fuel for the development of future sustainable drivetrains. By creating solutions aligned with current vehicle designs, the company is able to minimise complexity for OEMs and end-users, while using a basis of existing components where possible provides the maker with economies of scale possibilities and customers with reliability and durability equal to diesel.
“Hydrogen-fuelled internal combustion engines can meet the demands of the most challenging applications, providing the robustness comparable to a diesel engine to meet agriculture’s extreme operating and environmental conditions,” says Leitao. “The primary difference is in the machine’s on-board fuel storage. Through our joint venture with NPROXX, a specialist in high pressure hydrogen storage for both stationary and mobile applications, we are working to support OEMs with the development of storage tanks providing up to 700-bar pressure capability to maximise capacity.”
Solely ag
With a maximum power rating of 290hp (216kW) and 1,200Nm peak, Cummins says its B6.7H hydrogen engine is aimed squarely at the demands of agricultural tractors and other machines. Based on a next-generation Stage VI/Tier 5 platform, the engine’s base is unchanged from the six-cylinder block on the firm’s standard B6.7. Cummins calls the engine’s design ‘agnostic’, meaning it enables consistent mounting/space claim for clean diesel, natural gas or hydrogen fuelling infrastructure, and it is the cylinder head and fuel system that are chief differences.
“We believe hydrogen fuel cells can offer an efficient power solution for heavy-duty applications with high utilisation and energy demands, while meeting zero-emission needs, working alongside battery technology – ultra-capacitors, lithium-ion, or lead-acid – in a parallel hybrid set-up to deliver instantaneous response,” says Leitao. “We see hydrogen engines and fuel cells as complementary power sources offering different options to customers depending on where they are on their path to zero carbon. Introducing hydrogen engines in the market will also accelerate the growth of hydrogen infrastructure to support the widespread adoption of fuel cell powertrains.”
This article first appeared in the June edition of iVT International – https://ivt.mydigitalpublication.co.uk/june-july-2024