In this exclusive feature, Joe Forcash, automation and autonomy product manage at Caterpillar, discusses the company’s role in achieving increasing amounts of autonomy throughout the industrial sector
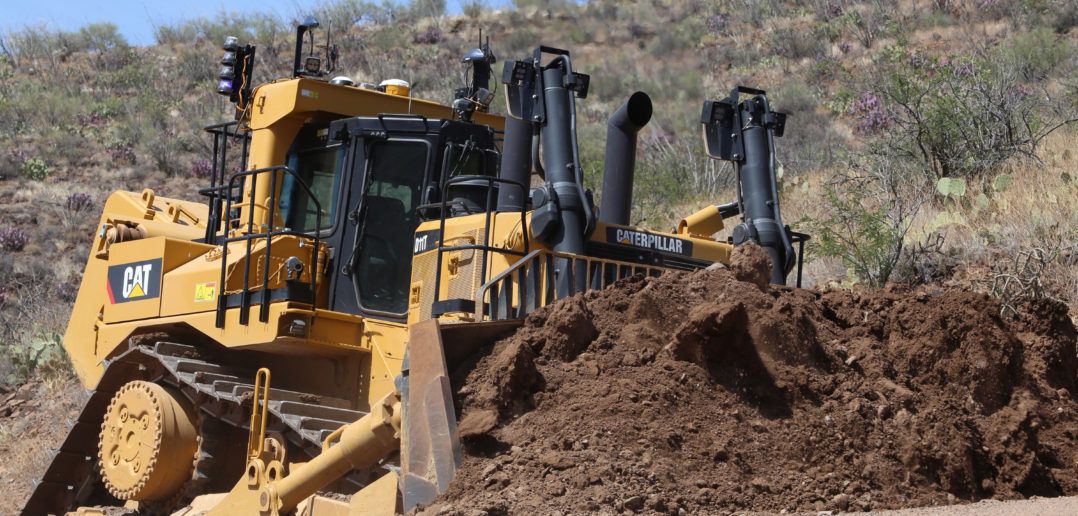
How is the development of autonomous technologies affecting the industrial vehicle industry?Â
Caterpillar provides industrial vehicles for both the mining and the construction industries. In mining, our customers are already utilizing our Cat Command systems, which provide both semi-autonomous and autonomous solutions. An example of our semi-autonomous solutions is the Cat Command for dozing technology that enables a remote operator to control multiple large dozers. The technology improves productivity and removes the operator from potentially hazardous environments.
One example of our autonomous solutions is Cat Command for hauling, which is an operating system for large mining trucks. No human operator, in the truck or located remotely, is required to control the truck. Truck scheduling and assignment is also fully automated. Command for hauling has achieved a 30% production improvement compared with standard trucks with operators onboard. Currently, there are 110 fully autonomous mining trucks operating in mines. The trucks have moved over 700 million tons of material safely over the last 5 years. We are continuing to expand the number of truck models capable of autonomous operation, and the number of mining companies deploying the system is growing.
In construction industries, we are creating evermore automated machine functions. Construction industry data shows a decline in productivity and a growing shortage of skilled operators. As a result, our current offerings focus on operator assist features to improve productivity by automating portions of the work cycle using Cat Connect technologies. For example, our recently introduced Next-generation excavators feature ‘Grade assist’, which automates boom, stick and bucket movements so operators can effortlessly stay on grade when digging.
Based on industry trends, the construction jobsite of the future will include fully autonomous vehicles. Caterpillar has been preparing for this for years, as we move from mechanically controlled to electronically controlled machines.
How do you think autonomous technologies will be used in industrial vehicles in the next 25 years?Â
In the short term, autonomous machines will be limited toward controlled sites. As demonstrated successfully with Cat Command for hauling, having multiple layers of safety is a requirement for deployment of autonomous vehicles. With more than five years of operating experience and 17 million miles (27.3 million km) driven by Cat autonomous trucks, there have been no lost-time injuries. As autonomous technology matures and further demonstrates its reliability, it will be deployed in less controlled sites.
It’s important to realize that the road to autonomous operations is a journey. The significant benefits of automation can be realized with even the simplest of applications. While full autonomy may be the ultimate goal, individual technologies can be used alone or combined in multiple ways to take advantage of immediate productivity, efficiency and safety gains and serve as the building blocks leading to autonomous operations.
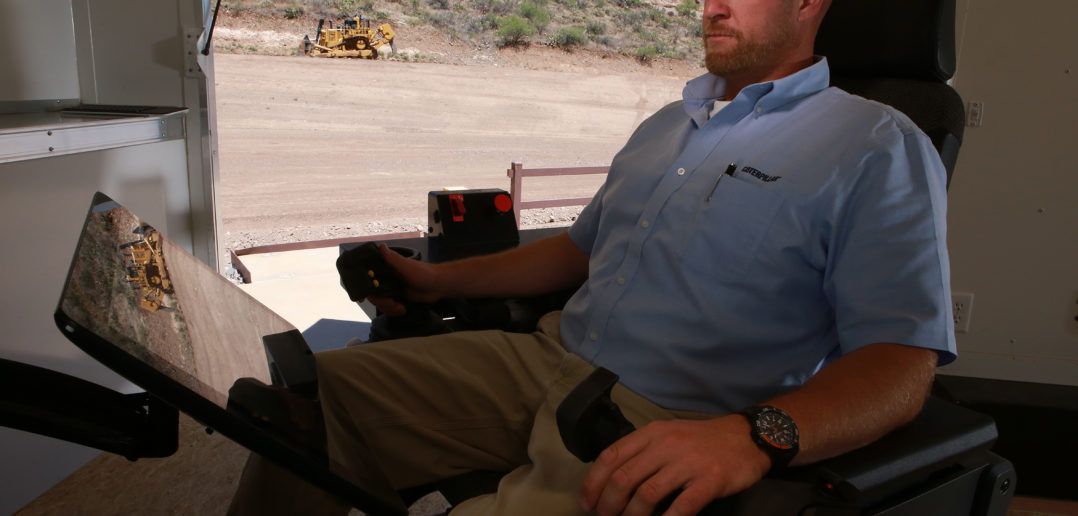
For example, we have rolled out some of the building blocks to autonomy in our Cat Connect solutions for construction industries. Our Cat Detect solution uses radar to detect people or objects in close proximity to the machine, and in these instances, the system alerts the operator. This application validates the technology for eventual use in an autonomous machine.
What do you think are the advantages and disadvantages of using autonomous technologies in industrial vehicles?
Caterpillar’s experience with automation is that it provides a step-change in safety. Additionally, mining customers have experienced significantly increased machine utilization due to virtual elimination of breaks and work shift changes. Because autonomous machines work in a very controlled manner with very little process variation, mining customers are experiencing significant production and cost improvements, too.
Do you think full autonomy (no use of humans) will be achievable in the next 25 years? – And why is this?Â
Full autonomy is achievable today on certain machines in specific applications. Cat Command for hauling is an example of a fully autonomous solution that our customers in mining successfully use today.
On the other hand, full autonomy for all machines in all applications is not likely in the next 25 years. Applications and tasks that are either dangerous or are relatively simple and repeatable are the most likely applications to be fully automated. But consider that machines working in the mining and construction industries are used to complete a wide variety of tasks in a range of applications. Many of our machines have multiple work tools that provide our customers the optimal solution to complete the job. Matching the technology to the right application is key to improving safety and productivity.

Following on from the previous question, if not in the next 25 years, then when do you think full autonomy will be achieved for industrial vehicles?
We (at Caterpillar) demonstrated our first autonomous truck at our Peoria Proving Grounds in 1985 (33 years ago). We went into production with our autonomous truck system in 2013. We demonstrated our first autonomous excavator in 1997 (21 years ago). We have been on a long autonomous journey. However, automation technology is changing at an ever-increasing rate. All we can predict is that automation will look very different in 25 years.Joe Forcash, automation and autonomy product manager at Caterpillar, shares his views on the impact of autonomy in the industrial sectors