iVT takes a trip to Volvo CE’s headquarters and proving ground in Ekilstuna, Sweden to get up close to its newly announced mid-size electric machines, with insight from the experts.
With a range of compact battery electric machines now firmly established, Volvo Construction Equipment (Volvo CE) has begun the next chapter in its electrification journey, with the announcement of two midsized wheel loaders, the L90 Electric and L120 Electric, alongside a new wheeled battery electric excavator and an electric, cable- connected material handler.
The first of these vehicles to be made available to market – from the fourth quarter of 2024 – will be the 20-tonne L120 Electric, which has a six-tonne lifting capacity. The L120’s smaller stablemate, the 15-tonne L90 Electric, said to be the first battery electric wheel loader in its class, will follow in selected European markets in 2025.
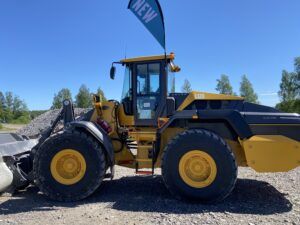
The design of the new electric wheel loaders has benefited from battery technology developed elsewhere in the Volvo Group. “It’s a Volvo electrification system,” says Fredrik Tjernström, Volvo CE electromobility solutions expert. “It’s executed with the same components as you find in battery electric Volvo Trucks.”
In terms of battery manufacturing, Volvo CE is taking a strategic approach to ensure quality and control over their electric machines. “There has been an evolution,” says Tjerström. “In the first compact machines we bought batteries as complete systems. But what you see in the new wheel loaders is the next level – we buy the modules, and then assemble the batteries in our own factories.”
This move towards in-house battery assembly gives Volvo greater control over the quality and performance of their electric machines. It also positions the company for future developments, with plans to eventually produce battery cells in-house.
“We have started to build our battery cell factory in Skövde, in between Gothenburg and Stockholm [close to Volvo Group’s main powertrain plant]. So that is the next step for us,” says Tjernström.
When the battery plant was announced in 2022 Martin Lundstedt, president and CEO of the Volvo Group said, “Our ambition is that at least 35% of the products we sell will be electric. This ramp-up will require large volumes of high-performing batteries, produced using fossil free energy and it is a logical next step for us to include battery production in our future industrial footprint.”
“It is a logical next step for us to include battery production in our future industrial footprint”
Electric transmission
One of the most significant innovations in the new wheel loaders is the dedicated electric transmission. “We’ve removed the converter, which caused a lot of energy losses in a conventional wheel loader, and electric motors are directly connected to the transmission,” says Tjernström. This not only dramatically improves energy efficiency but also enhances machine responsiveness and the overall performance.
The L90 and L120 Electric feature separate electric motors for hydraulics and propulsion, further optimising energy use and performance. “In a conventional wheel loader, you often drive or operate using one foot on the brake and one on the gas pedal,” says Tjernström. “Because if you want full hydraulic pressure to raise the bucket quickly, you step on the brake and push the throttle to build hydraulic pressure. But in the new electric wheel loaders there is no relation like that. So you can pull the lever hydraulic lever, and you will get full hydraulic power instantly. The accelerator pedal only controls the drivetrain.”
This decoupled system provides operators with instant hydraulic power and more precise control over the machine’s movements. While the new control paradigm may require some adaptation for experienced operators accustomed to traditional machines, it ultimately results in quicker response times, improved energy efficiency, and increased productivity through shorter cycle times, as well as a more intuitive learning curve for new operators.
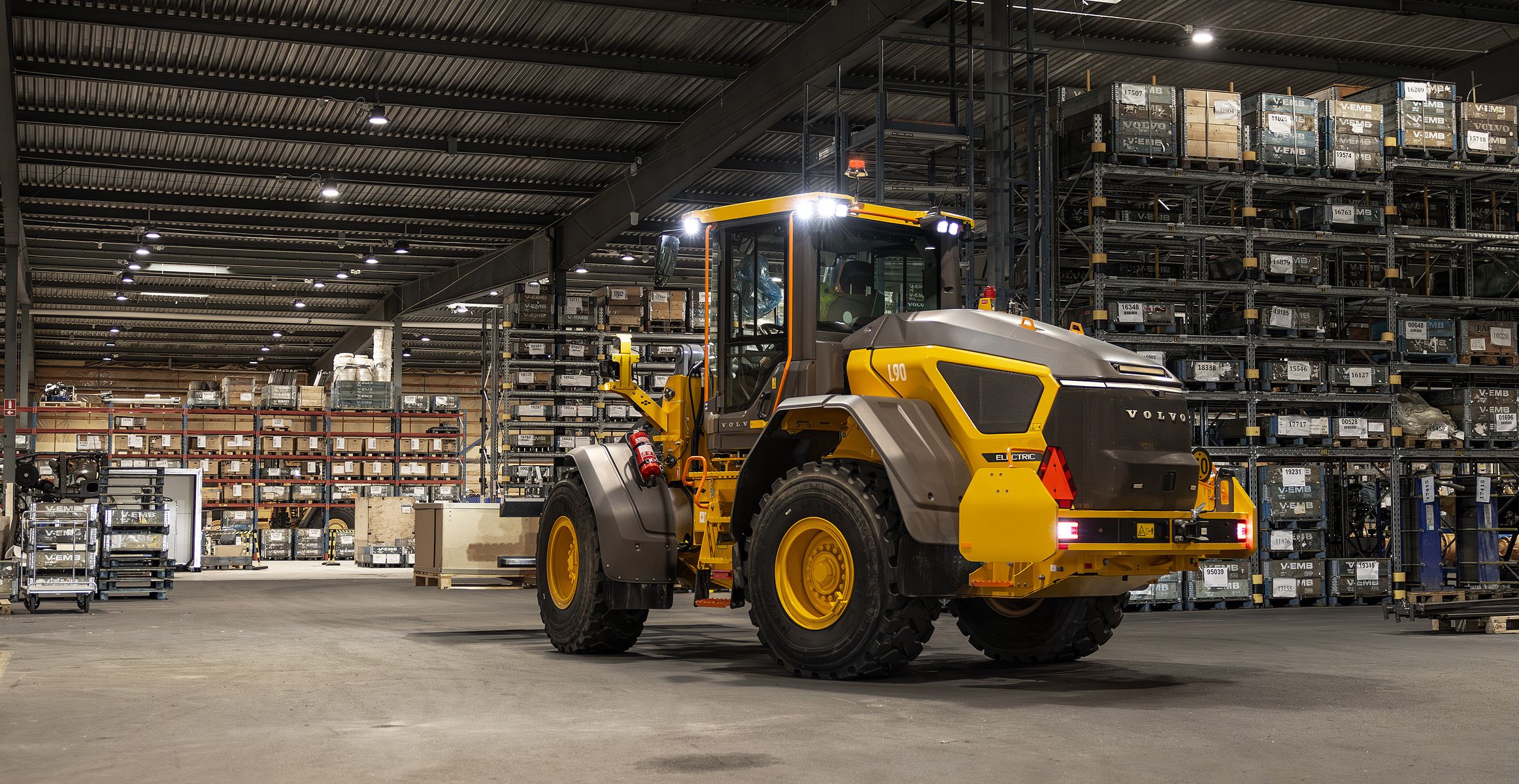
Matching diesel performance
A common concern with electric machines is whether they can match the performance of diesel counterparts. Volvo CE has addressed this head-on with the L90 and L120 Electric. “You can do the same work tasks with this machine,” says Tjernström. “The difference, of course, is the runtime.”
However, power autonomy levels are still impressive with the L120 Electric able to work a full day of around five to nine hours on a single charge, and the L90 Electric lasting for approximately four to five hours of medium duty operation. “The key is to plan your working day in such a way that you utilise non-productive time, using breaks to charge the machine,” says Tjernström.
To ensure maximum run time Volvo CE has put considerable thought and engineering into the battery technology, which is temperature-controlled, featuring both cooling and heating systems to ensure optimal performance, regardless of the climate. “We’ve done extensive customer tests in several sites in China, Dubai and Australia, with very positive feedback,” says Tjernström.
To enhance the ease of energy provision, the charging systems for the wheel loaders have been designed with flexibility and practicality in mind. They are compatible with existing charging standards, which reduces the barriers to adoption for companies looking to integrate electric machines into their fleets.
“You charge it with a CCS2 inlet, so that’s the same charging standards you have for cars or trucks,” says Tjernström, “So you can share the charging infrastructure on site with other equipment or vehicles.”
The L90 charges from 0-100% in about 70 minutes using a 150kW DC fast charger or Volvo’s PU500 mobile power unit, while its AC on-board cable can power up in six to seven hours for overnight charging. The L120 charges from 10-100% in one hour 40 minutes with a 180kW DC fast charger or the PU500 and in seven hours with a 40kW DC portable charger. Both wheel loaders also have recuperative ability, using braking energy when decelerating to charge batteries, ensuring a longer runtime and brake life.
Enhanced comfort and safety
The benefits of the new electric machines extend beyond the reduction in CO2 emissions. Tjernström points out the significant improvements in operator comfort and site safety: “They have a third of the noise of a similar diesel machines, but also a tenth of the vibrations. And that is really beneficial for operator comfort in the work environment.
“Operators often don’t think of the impact of noise and vibrations until they try it. But then they experience that they are not as exhausted afterwards as they are when they use diesel.”
The dramatic reductions in noise and vibrations also make the machines more suitable for urban environments and enclosed spaces, with the reduction in emissions beyond just carbon reducing immediate negative health impacts of diesel machines. “The NOx, particulate matter and all the other emissions are removed,” says Tejernström, “In an urban environment this reduces negative impacts to the health and well-being of the people in the city, as well as the operators.”
Electrification has also allowed for more advanced control systems and oftware integration. Operators can easily access functions and settings from the intuitive interface, which integrates the Volvo Co-Pilot and rearview camera when fitted.
Meanwhile, the machine’s powertrain, which was previously controlled by mechanical systems, is now managed by software. “Before it was a lot in valves and hoses,” says Tejernström “But now it’s controlled using software systems. This creates a new range of possibilities to remotely tune and customise the behaviour of the machine or the cooling system, or whatever.”
This software-centric approach allows for greater customisation and ongoing improvements through updates, extending the useful life and capabilities of the machines.
With the L90 and L120 Electric, Volvo CE is not just offering new machines; they’re providing a glimpse into the future of construction equipment – a future that’s cleaner, quieter, and more efficient than it has ever been before.
“It’s super-exciting,” says Volvo’s new director of technology Mats Sköldberg. “These machines will find applications where, from a total cost perspective, electrification can start to make sense for customers. Now we have the running hours, which mean the comparative cost of fuel in the diesel version will compensate their investment. We want to replace larger machines which emit more CO2 and thereby increase our impact.”
This article was first published in the August issue of iVT International