Flash Battery has launched its new laser-welding automated module assembly line.
The result of an investment of over €6 million, the new line is the core of the company’s recent headquarters expansion which added 2,200 square metres dedicated to a fully automated area for battery module assembly.
With an annual production capacity reaching 90,000 modules, this department is designed to house the entire welding and mechanical integration process within a controlled environment.
Flash Battery has chosen to internalize and develop all key process skills within its HQ: from its proprietary battery management system to mechanical and electrical design, process validation, and predictive maintenance.
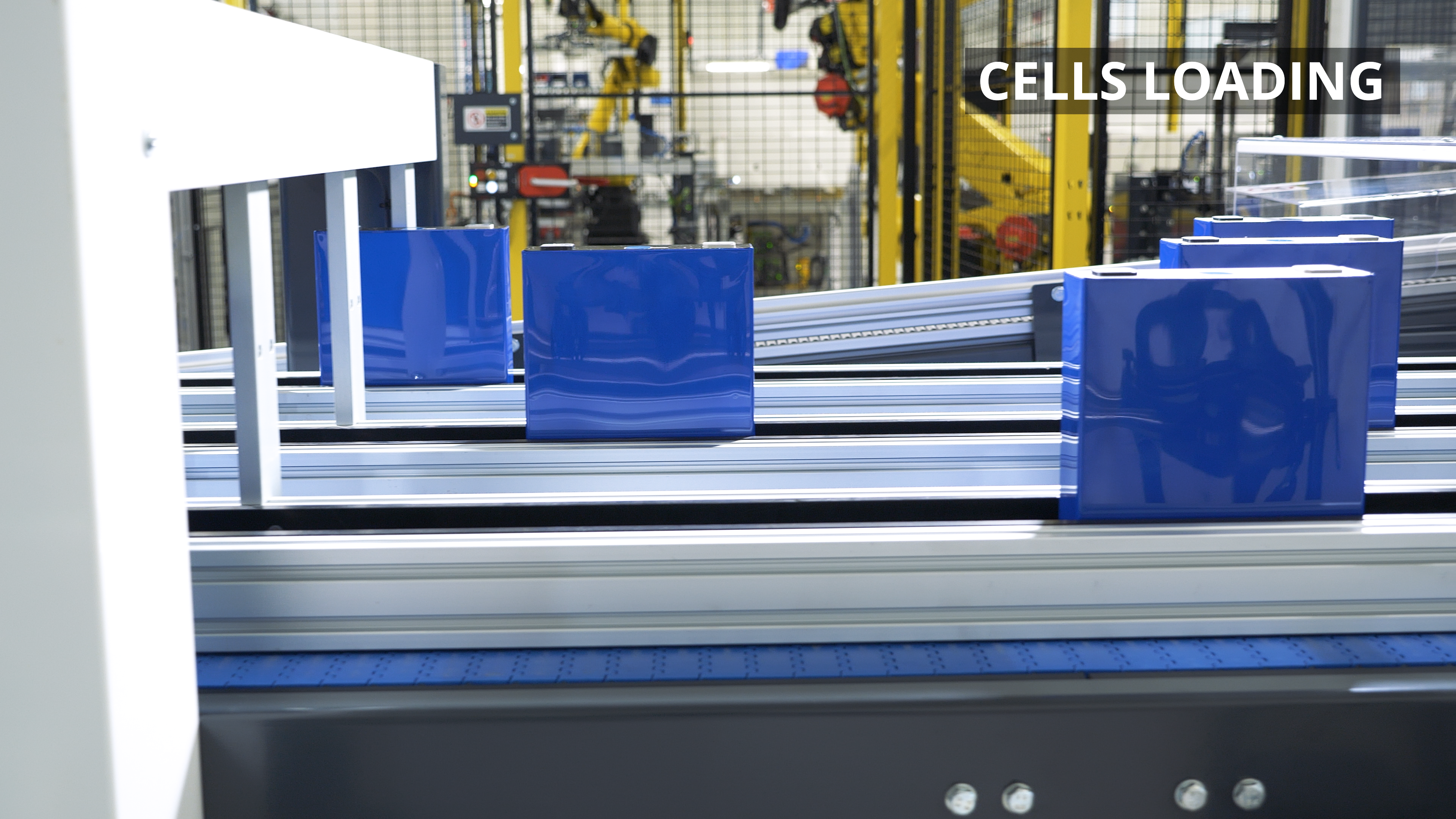
With the integration of this new module assembly line, the company finalizes its in-house production consolidation process, now also directly controlling welding and assembly activities previously outsourced to external suppliers. Except for the cells – sourced from top global manufacturers – every phase is now managed and supervised directly by Flash Battery.
This integrated management model allows the company to deliver fully tailored solutions aligned with each customer’s application needs, maintaining consistent standards of quality and performance, even in complex and dynamic industries.
“Bringing battery module assembly in-house means going directly to the source of the supply chain,” says Marco Righi, CEO and founder of Flash Battery. “For cells, we rely on leading global suppliers, selecting multiple providers for each type to increase supply chain reliability and enhance our negotiating power. Recent geopolitical and economic developments have confirmed the importance of having direct control over production to reduce lead times and supply issues.”
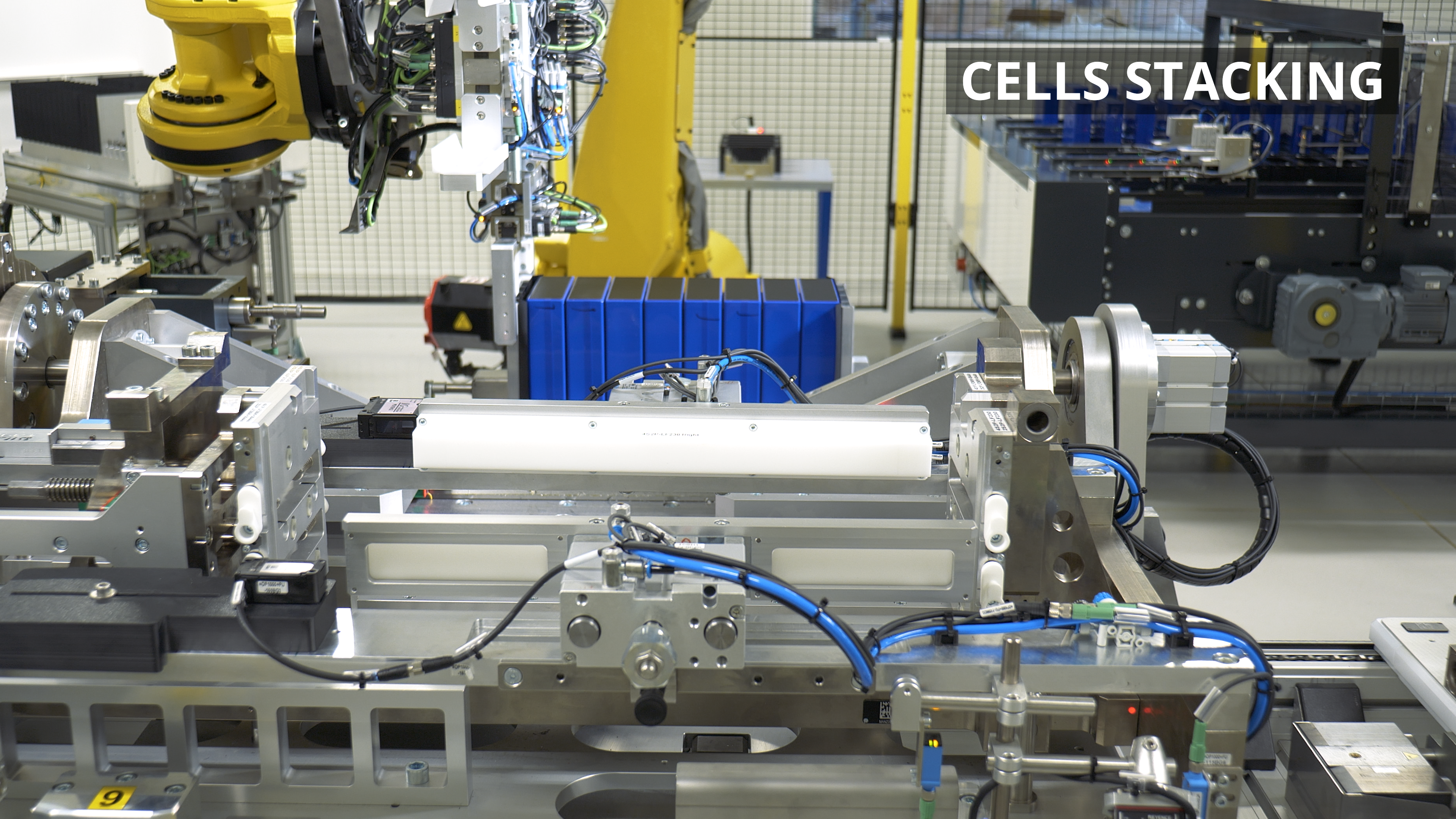
The new assembly line is engineered to quickly switch between configurations, managing 13 module variants with changeover times of less than 10 minutes. This enables Flash Battery to respond quickly and accurately to even the most specific customer requirements, supporting the creation of optimized electric systems without compromising on time or quality.
Laser welding ensures stronger mechanical and electrical joints, greater resistance to vibrations and lower energy dispersion. This is essential for achieving stable and reliable performance, particularly in demanding industrial applications.
The line operates through four core automated phases. The first is cell loading and automated inspection using optical inspection systems and high-precision sensors. Next is module formation with robotic stacking and placement of components into a containment structure for subsequent welding. Then, laser welding of frames and bus bars connect the cells for a durable and efficient electrical connection. Final compliance testing include safety, insulation, and mechanical resistance tests. Only modules that pass all tests are labelled and sent to Flash Battery’s battery pack assembly lines.
“With this new line, we are taking a decisive step toward a more autonomous, efficient, and reliable production model,” adds Marco Righi. “Integrating production skills allows us to respond promptly to customer needs and deliver tailored solutions with top-tier quality and performance. This is a key competitive advantage in a constantly evolving market.”
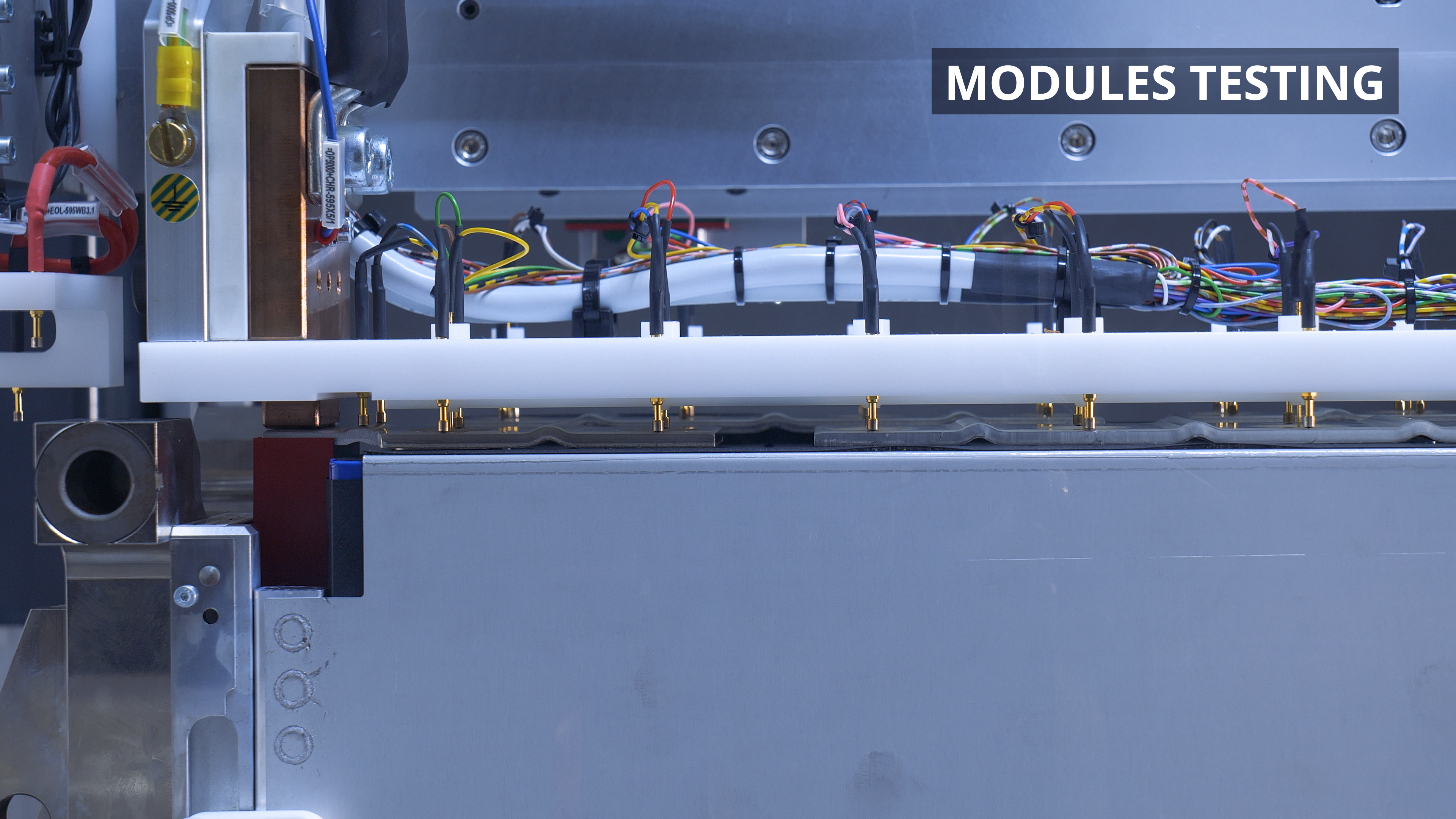
With this strong in-house autonomy, and the upcoming launch of European gigafactories dedicated to LFP (Lithium Iron Phosphate) cell – a safe, stable, and cobalt-free lithium technology – Flash Battery will soon be able to offer customers a fully European supply chain.
Images courtesy of Flash Battery