To reduce the risks of moving hot slag, OEMs Volvo CE and Liebherr have developed steel-mill wheel loaders specially adapted for the task – and in the process created the safest most durable vehicles in their class
Wheel loaders are essential machines across a variety of industries thanks to their adaptability for working with different materials. In steel mill environments, wheel loaders provide a crucial role to move hot slag. These impurities from steel making are removed from the furnace for reuse or repurposing into aggregates. Often likened to lava, this molten slag can be found at extreme temperatures up to around 1,200°C presenting a dangerous and high-risk working environment for the vehicle and its operator. As a result, many machinery manufacturers offer steel-mill specific wheel loaders to suit this extreme application.
“At Liebherr, customer satisfaction and safety are at the forefront of all solutions. For the work in this environment, safety and comfort are the top priorities for Liebherr wheel loaders. For this reason, there are various equipment options that reduce fatigue and enable safe and comfortable working,” explains Mark Walcher, product manager for XPower heavy equipment at Liebherr.
“Liebherr offers preparation for a protective ventilation system that filters particles and gasses and additionally seals the cab”
Driver safety
As well as intense heat, steel mills can be dusty and produce toxic fumes that would make it impossible for operators to work safely for extended periods of time. To combat this, wheel loaders for hot slag handling are equipped with specially designed cabs so the driver can breathe clean air.
“Liebherr offers preparation for a protective ventilation system that filters particles (e.g. soot, asbestos) and gasses and additionally seals the cab,” says Walcher. The driver is also protected by ballistic glass and a steel roof to prevent any sparks or splashes from seriously injuring them. Liebherr’s L 550 to L 586 XPower wheel loaders can be specified for slag applications.
At Volvo CE, its slag loader range, including L150H, L180H, L220H, L260H and L350H models, can be fitted with a cab filtration system which circulates 90% of cab air through a filter. While these solutions help to improve the driver’s daily job, machinery manufacturers also must equip slag handlers to cope with worst-case scenario situations. “The most important thing is operator safety,” says Erich Kribs, GPE product manager at Volvo CE. “If the machine stops inside of the steel mill, we want the operator to be in the machine for as long as possible.” Exiting the machine in these environments is likely to be more dangerous so Volvo has developed solutions for its slag handlers to allow the driver to stay in the cab if the machine breaks down. The driver is protected with a fire suppression system and an emergency limp home mode, which allows the operator to move the machine in first gear to give them an opportunity to move to a safer place to get help.
“If the operator is not available or they get sick inside of the cab, we have an engine shut down and parking brake release at the rear,” says Kribs. This means the vehicle can be moved from the outside without intervention from the driver if they are in difficulty.
Volvo CE also equips its slag loaders with a specialist towing point so another machine can retrieve the wheel loader by positioning its bucket under the hitch and lifting the back of the vehicle to tow it. Ordinarily, two vehicles would be manually hitched so this eliminates the need for an operator to exit their machine.
In the event the driver does need to exit the vehicle, Volvo CE offers an optional ladder which goes over the rear wheel arch. “Normally if there’s a problem with the machine in the steel mill, the front of the machine is standing in the hot area where the material is. The operator can leave via this escape ladder to the rear of the vehicle which is likely to be a safer area,” says Kribs.
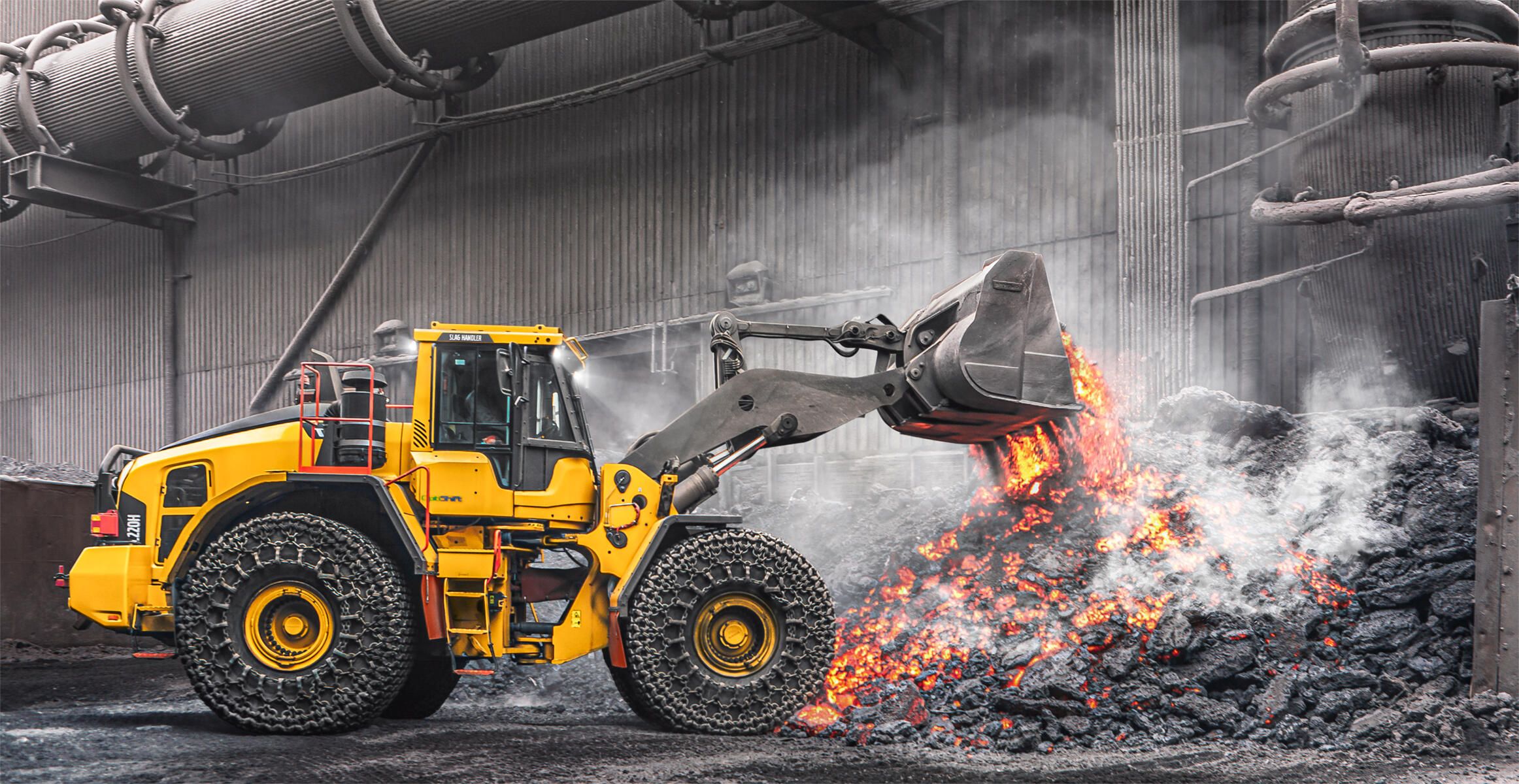
Key adaptations
Compared to a standard wheel loader, several components on a slag handler must be uprated for this high temperature environment. “Due to the challenging working conditions, the areas and components that are particularly exposed to extreme conditions must be protected accordingly,” says as Walcher. “These include hydraulic lines, piston rods, cables, underbody, electrical modules, central lubrication system and its lines, plastic parts and discs. Certain areas of the machine are equipped with an additional protective function. Components that are made of plastic in conventional applications, for example, are made of steel in this case to withstand the enormous heat.”
Some of these additional protections include steel mudguards, exterior steel mirrors, steel lamp holders, steel-braided hydraulic hoses, tipping cylinder piston rod protection and underbody guards. On top of this, some internal systems require the use of alternative materials. Kribs adds, “We have a different, fire-resistant hydraulic oil so if a hose cracks, the hydraulic oil will not start to burn. Also, the grease inside is more heat resistant for operating in these high temperature areas.”
“This is really what we need in special applications – working together with customers to get their feedback and find the best solution for everyone”
The challenges of testing
To make sure these adaptations are suitable for steel mills, machinery manufacturers must object their machines to extensive high temperature testing. Due to the extreme characteristics of a steel mill, it is hard to replicate these conditions in a lab or artificial setting. “To ensure that the wheel loaders are equipped for the special thermal conditions, the machines were tested in practical use,” says Walcher. “During this time, temperature measurements were taken in different areas of the wheel loader. Liebherr developed appropriate protective equipment based on the data collected.”
Similarly, Volvo prefers to conduct real-world testing, as Kribs highlights, “You cannot test something like hot slag in the free field, you need to go to a steel mill and find somebody who supports you. We are working with some key account customers who are happy that we are testing with them.”
Customer feedback is a crucial part of the development process for new attachments and parts, Kribs explains, “We are testing components like slag handling buckets with customers, we deliver parts or attachments, they test it and then say yes or no.” As well as input from the customer, Volvo CE regularly conducts site visits to measure certain aspects of the components. For a slag bucket, testing focuses on temperature and stress measurements
to analyse longevity and any potential weaknesses in the bucket.
“It is good to work together, this is really what we need in all special applications, to work together with the customer to get their feedback and find out what is the best solution for everyone. First, what is best for the customer, then what is best for us,” says Kribs.
While hot slag applications might not be the most common use for wheel loaders, these specialist adaptations are key in supporting steel mills and keeping operators safe. In high temperature environments, the industry cannot afford for a machine to be a fire risk or cause unplanned downtime. Slag handles are some of the most robust wheel loaders to enable mills to keep working around the clock.
This article first appeared in iVT’s 2025 Off-highway Annual.